Для того, чтобы правильно понимать ценность товара или услуги, нужно определиться с терминалогией. Существует мнение, что в условиях рыночной экономики термин «прибавочная стоимость» должен быть заменен на ценность товара.
Стоимость — это категория обмена, когда один актив меняется на другой. И это соотношение одного актива другому и есть стоимость. Менеджеры говорят: «Мы создаем стоимость». О чем речь, что это означает? Что означает понятие «добавленная стоимость»? Дмитрий Хлебников не без основательно считает, что на самом деле мы добавляем некую потребительскую ценность, то есть то, что важно потребителю и, что стоимость создать невозможно.
Терминология типа «добавленная стоимость» крайне популярна на постсоветском пространстве, что по мнению некоторых авторов скорее всего вызвано активным пропагандированием в прошлом учения К.Маркса и Ф.Энгельса.
Как можно видеть, речь идет о выгодах, полезности, преимуществах и т.д., но ни в коем случае ни о какой «стоимости». На русский язык дословно, с сохранением смысловой нагрузки, выражение added value перевести невозможно. Сам по себе продукт или услуга как набор кусков разных материалов или набор чьих-то действий никакого смысла для потребителя не имеют. Смысл для потребителя имеет ценность, которую несут в себе товары и услуги. Иначе говоря: любой продукт или услуга являются лишь носителями ценности, востребуемой потребителями. [2]
По такому принципу организован весь бизнес на Западе. Именно поэтому на любом западном предприятии нет лишних работ, услуг, станков, людей или чего-то другого. Они при организации бизнеса исходят из того, что их продукция кому-то нужна. И тем, что и в каком количестве нужно потребителю, определяется производственная цепочка.
Создание потребительской ценности -основополагающий концепции бережливого производства (Lean), в соответствии с которым целью ее использования является выявление и устранение потерь, не добавляющих ценности продукту и/или услуге с точки зрения клиента.
Система Lean (ЛИН) применяется во многих промышленных компаниях мира, а также в ЖКХ, армии, на транспорте, в сфере услуг.
Мировые производители работают по системе ЛИН уже более двадцати лет, из года в год повышая свою рентабельность. В России одним из первых предприятий, которое стало применять ЛИН, была автомобилестроительная компания «Группа ГАЗ», которой данная система помогла обеспечить конкурентоспособность без серьёзных капиталовложений.
Суть системы ЛИН заключается в трёх аспектах, представленных на рисунке.
Первый и самый главный шаг на пути к внедрению системы ЛИН - понять, что является ценностью для заказчика: качественная работа, скорость её выполнения или что-то иное. Для этого применяется анализ потока создания ценности, во время которого изучается бизнес-процесс в общем и определяется, на каком именно этапе действительно создаётся что-то ценное для заказчика. Если какие-то действия не создают ценности, их удаляют или меняют. Далее необходимо:
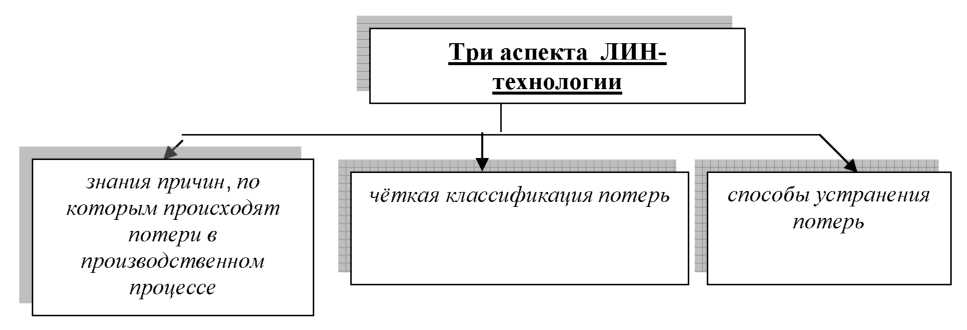
Три аспекта ЛИН-технологии
- Создать поток непрерывного движения от получения сырья до готовой продукции через специализированные производственные ячейки.
- «Вытягивать» продукцию, то есть следить за тем, чтобы она не находилась длительное время на складах, а сразу переходила в руки заказчика.
Виды потерь
Вид потерь |
Характеристика |
Влияние на ценность продукции |
1. Потеря творческого потенциала. |
Когда к сотруднику относятся как к винтику в механизме, который можно в любой момент выкинуть или заменить другим, когда отношения сводятся к схеме «работайте руками и строго выполняйте указания начальника», интерес сотрудников к работе неуклонно падает. Эксперты считают, что такой порядок вещей устарел, он тянет компанию назад, что не замедлит сказаться на прибыли компании. В той же Японии в различных компаниях появляются «кружки качества», на которых любой имеет право высказать свои предложения по улучшению качества процессов. Аналитики считают, что в XXI веке успех будет у тех компаний, которые смогут создать у своего персонала ощущение вовлеченности в совершенствование производства. |
Без отношения сопричастности, творческого рвения трудно выявить, создать, затем поддерживать ценность выпускаемой продукции |
2.Излишнее производство |
Выражающееся в том, что выпускается больше товара, чем требуется, либо раньше, чем требует заказчик. В результате те ресурсы, которые можно было потратить на улучшение качества, тратятся на увеличение количества. |
Одной из ценности продукции является поставка ее в срок. Опоздание как и предварительная поставка нежелательны. |
3. Задержки |
Когда рабочие простаивают в ожидании материалов, инструментов, оборудования, информации, это всегда следствие плохого планирования или недостаточно налаженных связей с поставщиками, непредвиденных колебаний спроса. |
|
4. Ненужная транспортировка |
Материалы или продукция перемещаются чаще, чем это нужно для непрерывного технологического процесса. Важно доставлять всё необходимое своевременно и в нужное место, а для этого на предприятии должны быть реализованы хорошие схемы логистики. |
Ненужная транспортировка обязательно отразиться на стоимости продукции,что в свою очередь снизит ее ценность. |
5. Неналаженные передвижения |
Плохо поставленный процесс доставки инструментов, материалов внутри самого предприятия, лишние передвижения сотрудников по помещениям. |
3. После первых двух действий начинать уже процесс усовершенствования: сокращать себестоимости площадей, уменьшать время для всех производственных операций и так далее.
Потери в любом производственном процессе -неизбежная проблема для многих предприятий, как производящих продукцию, так и оказывающих услуги. Потери - это состояние, которое, мягко говоря, не добавляет ценности продукту или услуге. Для того чтобы обнаруживать потери, сначала необходимо их распознавать. Специалисты системы ЛИН выделяют восемь видов потерь, из-за которых теряются до 85% ресурсов предприятия.
Карта потока создания ценности VSM (сокращение от английского Value Stream Map) - это достаточно простая и наглядная графическая схема, изображающая базисные показатели и взаимосвязь материальных и информационных потоков по созданию конечного продукта и/или услуги. Прежде всего, карта потока создания ценности позволяет глазами клиента увидеть как весь поток создания ценности «от двери до двери», так и отдельные процессы. [1] Это позволяет выявить проблемные области, связанные с потерями: например, деятельность, не создающую ценность с точки зрения клиента; лишние запасы сырья, незавершёнки и готовой продукции; потери времени сотрудников; неравномерности и перенапряжения потока создания ценности; некорректно организованную систему планирования и организации производства и т. д. Иногда при построении карт потока проводятся консультации с потребителями с целью выявления их фактических требований и пожеланий, чтобы потом принципы организации производства можно было согласовать в соответствии с этими требованиями. Ведь нельзя ориентироваться только лишь на собственное мнение о потребностях заказчика: известно, что достаточно часто компания производит продукции больше, чем фактически требует заказчик, при этом наделяя эту продукцию свойствами, которые не представляют ценности с точки зрения потенциального потребителя.
Продолжение таблицы |
||
6. Чрезмерные запасы |
Хранение на складах большего числа продукции, чем продаётся, и большего числа материалов, чем необходимо для технологического процесса. |
Приведенные виды потерь не позволяют снизить цену продукцию, а следовательно повысить ценность продукции. |
7. Излишняя обработка |
Продукция должна выходить из производства настолько качественной, чтобы по возможности исключать её переделки и доработки, а контроль за качеством должен быть быстрым и эффективным. |
|
8. Дефекты |
На улаживание претензий заказчиков уходят дополнительные средства: если необходимо исправить дефектное изделие, расходуются лишние время, силы и деньги. |
Следует помнить, что сама карта текущего состояния потока создания ценности не является самоцелью методологии VSM, она - инструмент анализа потока, обеспечивающий общий язык для принятия решений на всех уровнях компании и для дальнейшего воплощения их в жизнь. Поэтому, построив карту текущего состояния, ни в коем случае нельзя останавливаться на достигнутом. Следующим шагом работ по картированию является оценка состояния дел в ключевых областях потока, выявление основных проблемных зон и выработка оптимальных решений по их улучшению. После проведения анализа создаётся карта будущего состояния, показывающая варианты совершенствования с целью достижения более высокого уровня эффективности потока в некоторый момент времени в будущем. Параллельно разрабатывается детальный план реализации изменений по улучшению.
Иногда имеет смысл построить карту идеального состояния потока созданий ценности, задающую вектор поэтапных улучшений потока. На этой карте показывается состояние потока, которого можно достичь при комплексном развёртывании ЛИН-инструментов.
Таким образом, работа с картами потока позволяет повысить эффективность всей компании и избежать типичных ошибок выбора ЛИН-инструментов и областей их использования, которые обычно приводят к созданию малоэффективных изолированных зон улучшений.
Литература
- Вумек Д.П., Джонс Д. Бережливое производство: Как избавиться от потерь и добиться процветания вашей компании / Д.П. Вумек, Д. Джонс. 4-е изд. Серия Модели менеджмента ведущих корпораций. М., 2009. 477 с.
- http://www.aup.ru