When creating the concept of practical training for production system of JSC «Russian Railways’ a question arose what could be its foundation. Attempts to subordinate task of staff training in large companies to the interests of lean production (flexible in responding to market demand) do not always lead to success. This is confirmed, in particular, by data, cited in the article, collected from surveys of executives of the holding structures, which are held at the Corporate University of JSC «Russian Railways», as well as by the analysis of the experience of foreign companies and enterprises.
The general opinion of experts, the adopted approaches of the classical corporate training does not always meet the conditions of the time, it is necessary to look for new ways of knowledge transfer. The dynamics of the globalizing market is so high that the classical training system is not keeping pace with ongoing reforms, as traditional training is focused mainly on the transfer of knowledge, rather than on the audience involvement. They can hardly serve as an ideological influence on the audience, change their mindsets, train leaders. This contradicts the very idea of improving the production system.
The article the way how a new system of corporate training adapted to the interests and ideology of lean production was implemented. The article contains detailed review of approaches of lean production itself as well as authors’ conceptual approaches to the creation of a «system of lean learning», serving the needs of the lean production. The objective of the authors was to analyze advantages and disadvantages of lean learning system, using experience of the large foreign and Russian companies. Adaptation and debugging of learning processes, perhaps, are the most difficult issues in the practical application of the concept of lean production, and it is understandable. The development is impossible without a change of thinking, and it is also to be done, if the educational goals become such a comprehensive and responsible vector.
Background. The holding JSC «Russian Railways» modernizes its production system, implements modern technologies and management practices. A system of continuous staff training and development (see. Pic. 1) has been developed, in which various educational institutions interact. The system is constantly being improved in all areas of educational activities. In this article, we will focus on new approaches to business education of leaders of the holding structures.
Objective. The objective of the authors is to analyze advantages and disadvantages of lean learning system, serving the needs of the lean production, using experience of the large foreign and Russian companies.
Methods. The authors use analysis, statistical method, comparative method, evaluation method.
Results.
Focus on results
When creating the concept of practical training for production system of JSC «Russian Railways» a question arose what could be its foundation. The general opinion of experts was that adopted approaches of the classical corporate training does not always meet the conditions of the time, it is necessary to look for new ways of knowledge transfer. The problem is that the world has changed rapidly, today those companies benefit that keep pace with the changes taking place, increasing their efficiency. Now there is a change in economic structures [1], the traditional mass production is giving way to a lean, more efficient, active and flexible in terms of consumer demand. The dynamics of the globalizing market is so high that the classical training system is not keeping pace with ongoing reforms, thus ever more clearly revealing their drawbacks (see. Pic. 2).
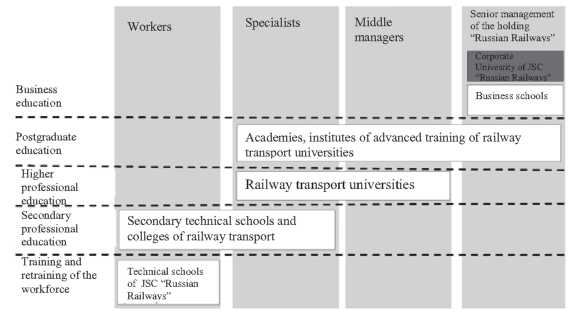
Pic. 1. A system of continuous staff training and development at JSC «Russian Railways».
1. Traditional training is focused mainly on the transfer of knowledge, rather than on the audience involvement. This is because the systems are built as formal[2], which are not designed for the bottom line, they can hardly transmit ideological influence on the audience, change their mindsets, train leaders. This contradicts the very idea of improving the production system: «If a company wants to change the workplace culture, it will have to raise its own leaders of lean production, which will implement and lead such cultural changes» [3]; «Lean systems are not just techniques and tools, but also philosophy. Speaking of lean systems, it should be understood that their philosophical component is primary, and the technology is secondary» [4].
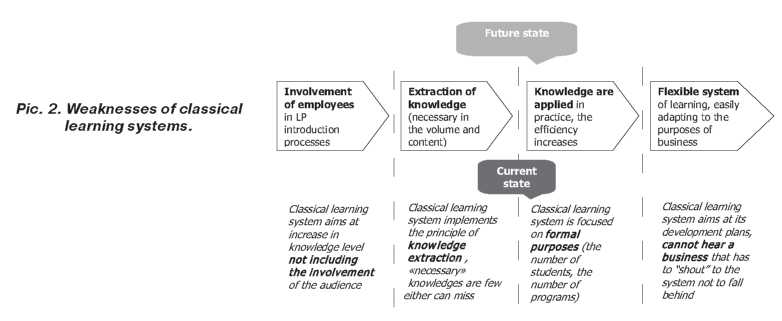
2. From the standpoint of lean production (hereinafter - LP) training in the traditional system looks like a mass production: the presence of parties (groups of students) and queues (schedule of training). This state of affairs occurs due to the fact that the training of parties allows providing for sure a maximum load of classrooms and teaching staff, reducing costs, including those intended for development of training programs. There are many disadvantages of mass production; probably the most important for us are ignoring the real demand, frequent disparity of educational process to the individual needs of students; large losses as a result of waiting for their turn. That is the traditional system of education, in terms of LP, is an old-fashioned formation, acting on the basis of ejection of products, which it produced.
3. Classical training of managers is not focused on business results. Its effectiveness is measured by the number of trained employees and studied programs. This is contrary to the objectives of the business, the main feature of the lean production [1] is «immediate feedback» as a radical reduction of labor costs, reducing to a minimum the work in progress, a significant reduction in production areas. If this result is absent - then, as western colleagues emphasize, you have hired the wrong sensei or the reason is your uncertainty.
4. The traditional system of learning is inflexible; it is hardly adapted to the changing demand from students, the conditions of the market environment. Stephen Covey in his book «The Seven Habits of Highly Effective People» [5] defines the concept of reactivity and proactivity. Reactive actions are acts committed under the influence of events, in fact, it is a reaction to the change occurred. Proactive actions are actions that determine events. Proactivity formula is: activity, initiative plus responsibility. Traditional learning systems are built as reactive. They lack of initiative, spend more time for adjustment to changing conditions, and therefore less effective. In terms of LP, it is unacceptable, experts require immediate results, the training system should be flexible, adaptive, and able to respond quickly to change.
Against the background of the drawbacks of traditional learning systems it is clear that it is necessary to organize learning on the principles of lean production, excluding losses in the creation and operation of the system. We have called this new learning system «lean» as we laid all the basic ideas of LP into it. Lean learning system (hereinafter - LLS LP) is designed to respond to the challenges in case when classical system «gives up».
Synthesis of the best practices
At the next stage the best practices were collected and the learning experience of LP was analyzed.
Masaaki Imai in his book «Gemba Kaizen: A Com-monsense, Low-Cost Approach to Management» [6] writes: «very important for us are Management Training Program (MTP) and Training Within Industries (TWI). These guidelines have come to Japan from the US, and their purpose was to assist the Japanese in developing their own training programs for managers and foremen. With «Management Training Program» middle managers were primarily trained, and on the basis of «Training Within Industries» foremen were trained. Management training program contributed to the fact that several generations of Japanese managers learned three concepts:
- The importance of human relationships and involvement of people.
- Methodology and the value of the continuous improvement of processes and products.
- The benefits of scientific and rational approach to people management and production operations, based on the method of «plan-do-see» approach».
Jeffrey Likerin «The Toyota Way: 14 Management Principles from the World’s Greatest Manufacturer» [3] gives two examples of conversion of a company into the lean enterprise. General Director Art Byrne of the Wiremold Company started with the fact that he began to conduct activities under kaizen. In another case, Keith Allman operated simultaneously in two ways: in person he conducted classes on LP and hired tutors to organize the model production lines.
The findings, made in the book, are important.
- Lean production is not studied by means of presentations in PowerPoint, at the beginning of reforms it is necessary to spend 80% of time on practice and only 20% of time on the theoretical training.
- All that was learned immediately should be practiced, and vice versa, what has been done in practice, should be explained in terms of theory.
According to Daniel Jones and James Womack [1] to learn the skills of working at lean production, we need a very special training. One of them (Jones) has consulted Unipart Group, United Kingdom about business transformation and the creation of Unipart Universite, which should be located not in a separate building, where we speak about off-job training, but right at the workplace. And tutors are line managers. Each training course should include only what is directly necessary to carry out the next step in the direction of lean production. People will be able to obtain new knowledge «just in time», that is precisely when they need it, and in the form that contributes to «do the right thing».
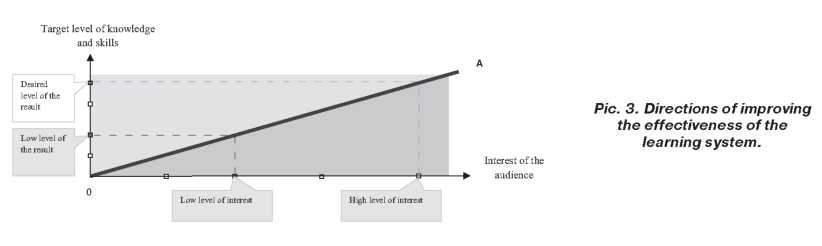
Russian experience in implementing LP is not big, but the leading companies in this field share their knowledge. Thus, A. A. Yagofarov, director of the business unit, a leading trainer consultant of SC «Orgprom» posted in his blog a post «On the dangers of teaching lean production». In the comments he gives the following estimate [7]: «there is some variability in the choice of learning strategies and damaging to Lean learning is a version when people are taught auditorily learning elements of LP, but there are no strategies for their practical application. In this case, the organization wastes material resources, and the people, who heard a lecture in the office, get an illusion that they know all, and for them it is «poorly applicable», «not applicable» up to «complete nonsense, working only in Japan».
The analysis of the weaknesses of classical systems of learning and the best practices of LP allowed making some generalizations:
- The new learning system must ensure the involvement of students in the ongoing transformation of the company and change of personal settings.
- In the organization of lean learning the principle of «just in time» should be used, achieving goal-oriented extraction of knowledge.
- The system is designed to be extremely flexible, capable of delivering new knowledge almost instantaneously into the workplace, controlling its acquirement and its correct application.
- LLS LP should be focused on the immediate business results of the student.
Thus, the creation of LLS LP should:
- Help managers to understand in practice and master the philosophy, technology, methods and tools of LP.
- Create a cohort of employees who believed in LP, and became its ardent supporters, who can really inspire, motivate and involve subordinates in the realization of the ideas of LP.
- Provide managers with the necessary knowledge and teaching materials for training and implementation of LP in the right place, at right amount and with right quality, right on time.
- Implement a competent project management of LP.
- Obtain the expected economic impact of successfully implemented LP projects.
Status of projects
Wanting to understand the current state of affairs in the field of LP, we conducted a survey of executives. The research at the Corporate University touched students of 2013 and 2014. Respondents included representatives of the 1st and 2nd levels of management according to the model of corporate competencies of JSC «Russian Railways». 554 employees were surveyed. Most of them work with the tools of LP four years, i. e. they are not novices, they had to have their own experience in implementing lean production ideas, big enough to understand the ideology of LP and to know how to use it. Four years would be enough to create a noticeable result, if a person is really involved in the process, rather than doing everything «under constraint».
On the question «What made you deal with LP?» 85% of managers responded that they were forced to do it, and 15% stressed their desire to engage in LP. It is natural to ask how you can inspire your subordinates with new topics, if you do not believe in it. In the sport psychology there is a term «congruence» (lat. congruens, - ntis - proportionate, appropriate). It is used to assess the ability of the athlete to achieve the best results. In business, there is also a need for a better result as compared with the competitors. Congruence is the balance between what a person says and what he thinks. Congruent leader will speak his subordinates that «LP is cool», and will think the same way, that is, he is really capable to light hearts, to involve employees in LP. Not congruent leader would take this constrained theme as «unnecessary headache», and will be talking out loud that «it is cool, it should be done». It is clear what «control effect» will be achieved in that case.
On the question of whether their subordinates want to engage in the implementation of LP programs, the majority of managers (77%) said they did not want to, and only 23% reported that their employees with interest considered the implementation of LP projects. It turns out that the employees are guilty, they «do not want». However, the problem has two reasons: the leaders themselves do not believe in LP, and are not able to mobilize subordinates. Therefore, in the training program an appropriate emphasis should be made.
Trying to understand the causes of ineffective implementation of LP, we asked the question: «How do you get the knowledge now?» It turned out that most of the leaders learn independently: 25% look for information on the Internet, 15% read books, some 15% - regulations, 10% - specialized magazines. When carrying out a written questionnaire in the accompanying interview we asked why this is so. The usual answers: we are forced to deal with it, but there is no knowledge, books and the Internet do not provide complete information. Those who have studied somewhere, were saying: «Yes, I attended a course, but all the examples on Toyota poorly correlates with our practice, they are not clear. And when at the workplace questions arise, there is nobody to ask, there is no place to get help, I lose heart”; «It is necessary to organize something, so I can ask an experienced expert».
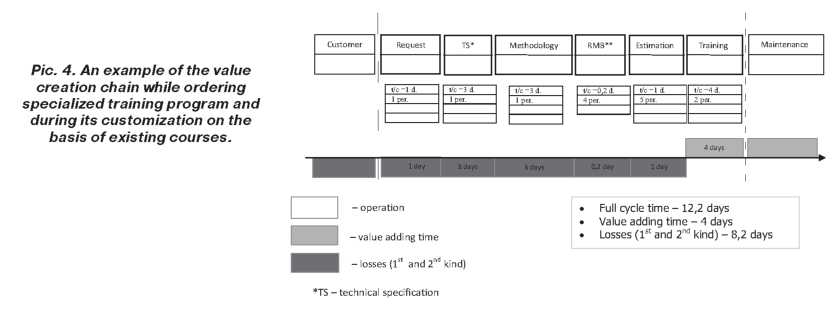
These words are confirmed by the answers to the question «What kind of support do you need to achieve maximum results?». More than half (54%) of executives believe that training is needed both to them and their subordinates; 46% advocate for additional resources, both financial and human. In addition, 62% said that learning is for them an extremely important factor in achieving success.
Summing up, we can say that many managers do not see any point in the implementation of LP, hence their low involvement. The first reason for this is lack of trust in the ideology of LP that may be a consequence of either poor training or lack thereof as such. The second reason is a lack of understanding, where to get qualitative material for the study of LP and get advice. This greatly discourages managers. The results will be much higher, and the resistance will be less if they get an address, pointlike attention, necessary knowledge, consultations during project implementation, if there are campaigns and examples that increase confidence in the methods and tools of LP.
Steps to create a learning system
Studies have shown that as it may, in the holding company there is a serious demand for LP learning. This demand and corporate strategic objectives are an incentive to create a system of lean learning. According to the order of JSC «Russian Railways» of January 23, 2015 N 122r project office is provided, which is called to build a lean production system. The plan of its activities includes:
- Support for ongoing programs and projects of organizational development.
- Optimization of regulatory and methodological documents regulating the functioning of the lean production system.
- Development of training programs of employees in methodical bases of lean production system of the holding.
We would like to illustrate the idea of lean learning by the example of the development of irrigation systems. Earlier frontal irrigation was applied, huge mechanisms moved slowly across the field, filling it with water. To reduce losses, a transition was committed towards drip irrigation. In this case, water is fed directly to the root portion of growing plants, and in the volume that is needed and when needed.As a result, the crop grows, ripens earlier, soil erosion and plant diseases are less.
By analogy, we can say that lean learning should be «drip». To understand how to do this, we define the basic concepts. Loss (muda) is any activity that consumes resources but does not create value [1] for the client. Value is something for which the customer is willing to pay.
In the irrigation example value is the amount of water delivered to the plant roots in exactly the right time in the right amount. Any deviation from the values, for example, increasing the water supply or irrigation after a rain, will lead to losses and harm the plant.
In this case, the value that should be created by LLS is the increase in efficiency of the activities of an employee after studying at the Corporate University. Losses are excessive or insufficient training, including unnecessary knowledge, not convenient or received at wrong time, etc.
In lean production there are five steps to create a lean enterprise [1]. This approach should be used for LLS. You need the following:
- Understand what value the learning system creates.
- Define each step in the creation of value and define loss.
- Ensure the continuity of the value stream.
- Learn how to respond to the individual needs of students by providing drawing of the value.
- Implement the ideology of continuous improvement.
The implementation of the first step is as follows. Here the value is revealed that LLS offers to the students. If the training is organized without a value, the system will provide only a formal purpose, audience will not understand, why they are trained, will not be able to apply the knowledge and will not bring the desired business results. Conversely, if the learning system works on the basis of the needs of students, it will be lean and lively [2].
Actions of the learning system are called live, if they are made on request from the audience. Actions without requests remain formal, or dead. In contrast to the traditional use of LP technology we face the fact that in the learning system the customer is at the center of the value production. As described in the best practices the consumer is outside the production, he only provides the order and carries out the acceptance of goods / services. This makes topical application of the concept of live training. Live actions of the system increase the involvement of students and lean actions reduce losses and focus on the obtaining of results. Together they create an effective system of learning.
Look at such an angle will allow differently see the value creation process, resources for improvement of the implementation of the knowledge gained. The more precisely the value is defined and the better it is represented, the higher is the interest of the audience. The greater is the interest of the audience, the better is the result - the target level of knowledge and skills (see. Pic. 3).
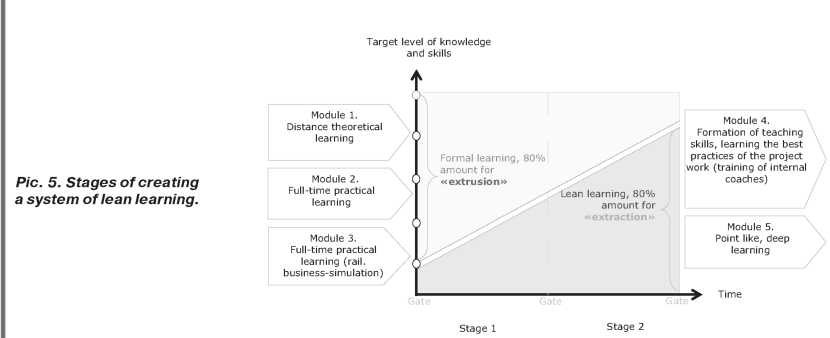
Differentiation of students by various levels of indicators such as the ability to learn and motivation to learn, will provide an opportunity to tune the learning system more precisely [8] for creating value. «The most effective way would be the selection of employees with the most pronounced cognitive characteristics, more educable and more interested in learning. This kind of projection of the Pareto principle would allow for the greatest return on truly creative and capable people» [9].
The source of knowledge must be the best corporate practices, the best international practices. It should also provide for cases where there is no information requested (for example, the students say «teach us how to apply such a LP tool in a certain professional field»). In such a situation, it is necessary to clearly understand who will conduct a research and develop the necessary knowledge at the right time, of the right quality, at a set cost.
In the second step it is necessary to determine each component in the value creation process [10], taking into account inevitable losses. In this case, all the acts committed in the learning system, can be divided into three groups:
- Actions that create value for the attendees.
- Actions that do not create value for the attendees, but which cannot be excluded from the process (muda of the first kind).
- Actions that do not create value for attendees and that can be excluded from the process (muda of the second kind).
To determine the losses associated with the process, it is required to create a value stream map (Pic. 4). Next, we remove the «extra» activities (muda of the second kind). Then we deal with the remaining actions, which do not create value (muda of the first kind), and only then we undertake the improvement of the processes that create value. For this purpose, methods of creating value stream, «extraction» and continuous improvement, which are described below, are used.
In the third step, we need to organize the stream movement. «It is not easy to apply the principle of stream to all activities, and not everything goes right. Initially it is generally very difficult to learn to see the value stream and understand the full value of the stream. When such a vision arises, there are new challenges to overcome» [1].
Taiichi Ohno believed that the principle of «just in time» will ensure continuity of the value stream creation, it is necessary that the work in all areas will be concerted, and the timing of its execution will be exactly equal to the takt time. The principle of «just in time» -is «a way to make the production work for the company as the human body works for its owner» [11].
It is also worth mentioning that in the organization of the stream movement the system poka yoke (protection against accidental damage), visual inspection methods (5S, «andon”), alignment are used.
The training system should also learn how to quickly rebuild (quick changeover) upon request of listeners, making new knowledge for them.
The fourth step. Knowing what students want, creating a continuous stream of knowledge (values), it is necessary to provide their extraction. Students should receive the necessary knowledge and experience in the relevant time for them, with right amount, quality, location. This requires not only a system for collecting information about the needs for knowledge, but also a system of knowledge in the workplace; only in some cases off-job training is acceptable.
When the lean learning is launched, the potential audience is willing to learn, and some part is not ready yet. Both groups have to learn. The fact that there are some students, not ready «to buy» service, makes the introduction of LLS an exceptional phenomenon. It turns out that it is necessary first to create a demand, and only then to give knowledge. «You can lead a horse to water but you cannot make it drink» (English proverb). In the designed learning system, this problem can be solved through coordinated work in two modes: extrusion and extraction (Pic. 5). One of them accelerates, the other picks up and ensures a continuous and stable motion.
Different modes of learning are caused by different types of tasks. Part of the holding units already moves towards the implementation of LP, they have a basic understanding of its tools and principles; they have some experience in project implementation. They need answers to practical questions, they are ready to ask. For them, the training system should operate in «extraction» mode. It begins to run at full speed when the listeners get interest and involvement, and most importantly - they have reached certain (albeit small) business results.
On the other hand, there are units that have not started LP or are just beginning to implement it. Their basic need is to get some basic knowledge of «what to do?». For them, the learning system is configured to operate in the «extrusion» mode. The purpose and at the same time the result is the provision of basic knowledge, clarifying technology, mentoring, conducting a training, the emergence of interest in the tools and principles of LP. Daniel Jones and James Womack said about the need for such an approach: «one of the paradoxes of lean production - is that its democratic ideas are completely contrary to the old hierarchical system... That is why efforts are required to get people to see and try out what seemed delirium for them before that» [1].
It is important to emphasize again that the learning should follow the practice, that is, students must first face the problem of implementation, then they have to dive into it, then the initial demand arises that can be satisfied, for example, by means of remote learning courses, databases, consultations with experts etc. Only in some cases, they can request a full-time education. The variety of complementary forms will increase the flexibility of the system, there will be more coverage of employees, costs for training will reduce, and its efficiency will improve. And this occurs despite the fact that the provision of the system improvement of the competences of employees in full-time mode would also be clearly not «lean» [12].
The fifth step involves the continuous improvement of the learning system. «In the traditional management environment the concept of excellence through ongoing improvements is taken very seriously. But it is a fundamental principle of lean thinking!.. It is sad to acknowledge, but we saw a lot of organizations that at the beginning had the vision and energy. But they have little or nothing, as the desire to improve all that is possible, led to a dissipation of limited resources in a thousand different directions. We must act differently» [1].
The improvement will be much more efficient if we are guided by LP method- policy deployment (in Japanese - hoshin kanri). According to it, it is necessary to set simple goals, to establish projects to achieve them, to determine time, resources, and quantitative indicators. It helps to have a clear action plan and to focus on the most important areas of production.
Conclusion. Adaptation and debugging of learning processes, perhaps, are the most difficult issues in the practical application of the concept of lean production, and this is understandable. It is necessary to solve a difficult problem to generate a demand, to gradually replace extrusion with extraction; to define and to eliminate consistently all losses, to achieve a situation where the training will be perceived as a very effective way to solve business projects. The development is impossible without a change of thinking, and it is also to be done, if the educational goals become such a comprehensive and responsible vector.
REFERENCES
- Womack, James P., Jones, Daniel T. Lean Thinking: Banish Waste and Create Wealth in Your Corporation [Russian edition, translatedfrom English]. Moscow, Alpina Publisher, 2013, 472 p.
- Gaidukov, A. M. Live and other systems of corporate learning [Zhivye i ne ochen’ sistemy korporativnogo obucheniya]. Korporativnye universitety, 2013, Iss. 43, pp. 3-10.
- Liker, Jeffrey K. The Toyota Way: 14 Management Principles from the World’s Greatest Manufacturer [Russian edition, translatedfrom English]. Moscow, Alpina Business Books, 2005, 402 p.
- Liker, Jeffrey K., Meier, David. The Toyota Way Fieldbook: A Practical Guide for Implementing Toyota’s 4Ps [Russian edition, translated from English]. Moscow, Alpina Business Books, 2006, 588 p.
- Covey, Stephen R. The Seven Habits of Highly Effective People [Russian edition, translatedfrom English]. Moscow, Alpina Publisher, 2014, 396 p.
- Masaaki Imai. Gemba Kaizen: A Commonsense, Low-Cost Approach to Management [Russian edition, translatedfrom English]. Moscow, Alpina Business Books, 2005, 346 p.
- http://www.leanforum.ru/expert96/blog/message369.html. Last accessed 11.02.2015.
- Alchebaev, M.A., Gaydukov A. M. Gamification or Mystification? World of Transport and Transportation, 2014, Vol.12, Iss . 3, pp.220-228.
- Steblyanskiy, N. V. Corporate Continuing Education. World of Transport and Transportation, 2009, Vol.7, Iss.3, pp.156—159.
- Rother, Mike, Shook, John. Learning to See: Value Stream Mapping to Add Value and Eliminate MUDA [Russian edition, translatedfrom English]. Moscow, Alpina business books, 2008, 144 p.
- Taiichi Ohno. Toyota Production System: Beyond Large-Scale Production [Russian edition, translated from English]. Moscow, ICSI, 2005, 192 p.
- Gapanovich, V. A. Lean production at JSC «Russian Railways» [Berezhlivoe proizvodstvo v OAO «RZhD»]. Zhelez.nodoroz.hnyj transport, 2012, Iss. 4, pp. 15—18.
- Meier, David, Liker, Jeffrey K. Toyota Talent: Developing Your People the Toyota Way [Russian edition, translated from English]. Moscow, Alpina business books, 2008, 304 p.
- Steblyansky, N. V. The development system of top management of a large corporation (the experience of JSC «Russian Railways») [Sistema razvitiya top-menedzhmenta krupnoy korporatsii (opyt OAO «RZhD»)]. Menedzherpo personalu, 2012, Iss. 4, pp. 6—13.
- George, Michael L. Lean Six Sigma for Service: How to Use Lean Speed and Six Sigma Quality to Improve Services and Transactions [Russian edition, translatedfrom English]. Moscow, Mann, Ivanov and Ferber, 2014, 464 p.
- Womack, James P., Jones, Daniel T. Lean Solutions: How Companies and Customers Can Create Value and Wealth Together [Russian edition, translatedfrom English]. Moscow, Alpina Publisher, 2014, 264 p.
- Dennis, Pascal. Lean Production Simplified. A Plain Language Guide to the World’s Most Powerful Production System [Russian edition, translated from English]. Moscow, Olimp-Business, 2013, 224 p.
- Rother, Mike. Toyota Kata: Managing People for Improvement, Adaptiveness and Superior Results [Russian edition, translatedfrom English]. St. Petersburg, Piter publ., 2014,336 p.
- Art Byrne. The Lean Turnaround: How Business Leaders Use Lean Principles to Create Value and Transform Their Company. McGraw-Hill. 2013, 225 p.