Недавно под председательством старшего вице-президента ОАО «РЖД» В.А. Гапановича состоялась очередная видеоконференция, посвященная внедрению проекта «Бережливое производство в ОАО "РЖД”». Было отмечено, что принципы бережливого производства охватили все направления развития отрасли. Но чтобы добиться мультипликативного эффекта, этот позитивный опыт нужно распространять как можно энергичнее.
Проект «Бережливое производство» начался в ОАО «РЖД» в 2010 г. Тогда в нем участвовали всего 27 пилотных предприятий. В то время еще отсутствовала методология внедрения технологий бережливого производства на железнодорожном транспорте. За прошедшие два года многое изменилось. Сейчас число предприятий-участников проекта — приближается к тысячи. Во многих предприятиях разработана нормативная база, определены показатели и критерии оценки эффективности внедрения технологий бережливого производства, мотивационные механизмы, программы обучения. Применены проектные подходы к управлению процессом внедрения технологий бережливого производства в функциональных филиалах производственного блока.
Важным этапом распространения проекта «Бережливое производство» стало утверждение президентом ОАО «РЖД» В.И. Якуниным положения о ежемесячном проведении «Дня качества». Начиная с августа 2012 г., были проведены такие Дни, посвященные качеству инструмента, применяемого в подразделениях производственного блока, метрологическому обеспечению средств измерений, совершенствованию технологии работ, а также обучению работников и качеству технических занятий.
Эксплуатационный локомотивный комплекс вошел в проект «Бережливое производство» в ОАО «РЖД» в 2012 г. К внедрению проекта были подключены 19 структурных подразделений в восьми региональных дирекциях. Рабочие группы созданы в Дирекции тяги, регионах и эксплуатационных локомотивных депо. Определены приоритетные направления деятельности по снижению непроизводительных расходов в эксплуатационном локомотивном комплексе благодаря внедрению инструментов бережливого производства. Основное внимание уделяется сокращению подготовительно-заключительного времени локомотивных бригад за счет оптимизации маршрутов перемещения от места явки или отдыха к месту приемки локомотива, оптимизации маршрутов при прохождении предрейсовых процедур, изменению технологии постановки локомотивов в депо, выдачи из депо.
По итогам 2012 г. принято к внедрению более 30 проектов по трем основным направлениям, получен экономический эффект не менее 10 млн. руб.
Приоритетными направлениями по снижению непроизводительных расходов в эксплуатационном локомотивном комплексе благодаря внедрению инструментов «бережливого производства» определены:
- сокращение подготовительно-заключительного времени локомотивных бригад путём оптимизации маршрутов перемещения от места явки или отдыха к месту приемки локомотива, оптимизации маршрутов при прохождении предрейсовых процедур, изменения технологии постановки локомотивов в депо, выдачи из депо. В качестве примера можно привести проект, внедренный в депо Нижнеудинск Восточно-Сибирской дирекции тяги, по оптимизации процесса подготовительно-заключительных операций при отправлении поездов благодаря использованию для ввода/вывода локомотивов из депо и маневровых передвижений по путям станции локомотивных бригад прогрева;
- снижение доли непроизводительных потерь рабочего времени локомотивных бригад (следование пассажиром, переотдых в пунктах оборота) благодаря постоянному улучшению технологии их работы. Примером данного проекта служит разработанная технология в депо Калининград по снижению потерь рабочего времени локомотивных бригад за счет организации пунктов заступления на станциях Балтийск и Балтийский Лес, что отменило необходимость следования бригад пассажиром к месту приемки локомотивов на данных станциях из основного депо Калининград;
- оптимизация использования бюджета времени локомотивов. В том же депо Нижнеудинск сократили время, необходимое для постановки локомотива в депо. Эффект достигнут за счет оптимизации маршрута следования (врез дополнительной стрелки) и алгоритма согласования номера пути, на который становится локомотив;
- снижение непроизводительных расходов топливно-энергетических ресурсов, в том числе на «горячий простой». Примером здесь служат внедренные проекты челябинцев по порядку отстоя локомотивов в депо и златоустовцев из Южно-Уральской дирекции тяги по порядку применения режима рекуперации на электровозах ВЛ10.
Если остановиться на опыте нижнеудинцев, то можно отметить следующее. Специалисты депо изменили технологию подготовительно-заключительных операций по отправлению поездов со станции Нижнеудинск. Она представлена в таблице. Экономия показана на рис. 1.
Для получения таких результатов пришлось выполнить ряд преобразований. Так, чтобы исключить потери в использовании времени локомотивных бригад на получение предупреждения формы ДУ-61 у дежурного по парку и дальнейшее следование от дежурного по парку до локомотива, решили для выдачи данного документа разместить в помещении дежурной смены депо работника станции.
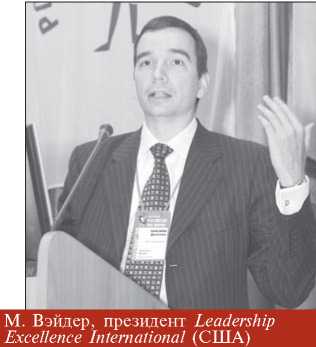
Рис. 1. Анализ процесса отцепки локомотива после изменений в технологии явки локомотивной бригады
Общее время трудозатрат |
Время, добавляющее ценность |
Время, не добавляющее ценность |
76,5 минуты |
35,5 минуты (46,4%) |
41 минута (53,6%) |
Анализ процесса отцепки локомотива после изменений в технологии явки локомотивной бригады
Эффект от операции |
Операция |
Время шага, мин |
ДЦ |
Предрейсовый медосмотр |
5 |
ДЦ |
Инструктаж (ознакомление с приказами, указаниями) |
5 |
НДЦ |
Получение машинистом маршрута, указаний дежурного по депо, предупреждения об огра-ничении скорости, документов от дежурного по парку (в помещении дежурной смены депо) |
2 |
НДЦ |
Следование в четный парк |
12 |
ДЦ |
Приемка локомотива |
19 |
ДЦ |
Заправка скоростемера диаграммной лентой (установка кассет регистрации) |
2 |
ДЦ |
Зачистка писцов (настройка параметров кассет регистрации) |
2 |
ДЦ |
Проверка действия и осмотр устройств локомотивной сигнализации, автостопа, электронных приборов безопасности |
1,5 |
НДЦ |
Сокращенная проба тормозов |
16 |
ДЦ |
Получение справки ВУ-45 о тормозах |
1 |
НДЦ |
Регламент минутой готовности перед отправлением поезда |
1 |
НДЦ |
Отправление по команде ДСП |
10 |
Примечание: ДЦ — время, добавляющее ценность;
НДЦ — время, не добавляющее ценность.
Потери рабочего времени локомотивной бригады и простой поезда на станции, связанные с полным опробыванием тормозов, составлял до 30 мин. С установкой УЗОТ потери рабочего времени сократились до 10 мин.
В эксплуатации при формировании сдвоенного поезда возможен неподход автосцепок между хвостовым вагоном первого поезда и локомотивом второго поезда. Чтобы это избежать, вагонникам предложено использовать линейку для замера высоты автосцепки хвостового вагона первого поезда. В результате исключены отмены сдвоенного поезда и двух локомотивных бригад.
Большое внимание уделяется снижению потерь рабочего времени локомотивных бригад (следование пассажиром, переотдых в пунктах оборота) благодаря постоянному внесению улучшений в технологию их работы. В некоторых депо локомотивные бригады работают по именным графикам. Также проводится оптимизация использования бюджета времени локомотивов усовершенствованием системы планирования ТО-2.
Наряду с этим внедряется технология полигонной работы, уменьшающая в цикле эксплуатации локомотива долю процессов, не создающих добавленной стоимости (пересылка, ожидание технического обслуживания или ремонта), приводятся в соответствие с выполняемой работой количество и серии локомотивов, обслуживающих участок.
Важное место в работе придается снижению непроизводительных расходов топливно-энергетических ресурсов, в том числе на горячий простой и уменьшение числа отказов технических средств благодаря тщательному расследованию причин их возникновения. Определены основные показатели оценки эффективности внедрения инструментов бережливого производства и их значения для каждого локомотивного депо. Разработаны предложения по мотивации работников.
Внедрение технологий бережливого производства на предприятиях Дирекции тяги осуществляется в соответствии со стратегией инновационного развития ОАО «РЖД» и корпоративной системой управления качеством. В связи с разделением локомотивного комплекса на ремонтную и эксплуатационную составляющие основная часть эксплуатационных расходов приходится на оплату труда, топлива и электроэнергии. Это ясно указывает на решение каких вопросов в первую очередь должны быть направлены инструменты бережливого производства.
Поэтому основная деятельность дирекции по повышению эффективности с использованием инструментов бережливого производства должна быть направлена на:
И пересмотр технологии работы в каждом локомотивном депо (изменение плеч, подвязки, перенос пунктов предрейсового медицинского осмотра, мест явки);
И экономию топливно-энергетических ресурсов при горячем простое;
И использование электрического торможения;
И внедрение современных диагностических комплексов для контроля работы тягового подвижного состава;
И повышение качества эксплуатации локомотивов за счет выбора рациональных режимов, исключения перегрузок;
И уменьшение перепростоев локомотивов на плановых видах ремонта.
Хотелось бы отметить еще один передовой опыт в области бережливого производства. Включившись в проект «Бережливое производство», эксплуатационное депо Челябинск поставило перед собой задачу сокращения расхода электроэнергии и дизельного топлива на горячий простой электровозов ЧС7 и тепловозов 2ТЭ10 за счет оптимизации производственного процесса. Картирование осуществлявшихся в депо процессов подготовки локомотивов к работе позволило выявить имевшиеся потери и наметить пути их сокращения.
Так, простой электровозов ЧС7 в горячем состоянии (с поднятыми токоприемниками) составлял в среднем 15 ч 23 мин. За счет использования на данных локомотивах устройств подогрева масла в картере компрессора и обогрева кранов главных резервуаров простой с поднятыми токоприемниками удалось сократить до 1 ч 44 мин летом и 2 ч 4 мин зимой. Был налажен контроль состояния электровозов при отстое.
Простой тепловозов 2ТЭ10 в горячем состоянии составлял в среднем 14 ч 31 мин. Благодаря сливу воды из водяной системы тепловоза и полного его расхолаживания, простой в горячем состоянии сократился до 1 ч 48 мин. Слив воды из системы выполняют квалифицированные работники пункта технического обслуживания (ПТО) тепловозов.
Чтобы отслеживать потери электроэнергии и дизельного топлива на каждом этапе отстоя и оперативно устранять причины потерь, установлены точки контроля процесса. Машинист, прибывший на локомотиве в депо, записывает показание счетчика электроэнергии (или данные о количестве дизельного топлива в баках) в бортовой журнал и маршрут машиниста. Машинист экипировки, принимающий локомотив, проверяет правильность записей и расписывается в маршруте прибывшего машиниста.
После выезда локомотива из ПТО машинист экипировки перегоняет его на пост отстоя локомотивов и там передает показания счетчика электроэнергии машинисту экипировки поста или помощнику дежурного по депо, делая соответствующую запись в журнале формы ТУ-152. Машинист экипировки поста отстоя локомотивов или помощник дежурного по депо передает показание счетчика электроэнергии машинисту, принимающему локомотив. Разницу между последним показанием счетчика и показанием, записанным в бортовой журнал, дежурный контрольного поста (КП) фиксирует как расход под депо и расписывается в маршруте принимающего машиниста.
Годовой экономический эффект ожидается в размере более 4,5 млн. руб.
В текущем 2013 г. в соответствии с утвержденным распоряжением состав структурных подразделений, участвующих в проекте «Бережливое производство», увеличен в 3 раза. В работу включаются все территориальные дирекции и 57 локомотивных депо. Планируется внедрить более 100 проектов и мероприятий с экономическим эффектом не менее 795 млн. руб. При этом данный эффект отражен в Программе по оптимизации расходов филиалов ОАО «РЖД» по разделу «Организационно-технические мероприятия». Для этого Дирекция тяги ставит задачи по вовлеченности в проект не менее 25 % инженерного и командного состава всех депо. Стационарные рабочие места на предприятиях, вовлеченных в проект, должны отвечать принципам 5S.
Для выполнения поставленных целей намечены следующие мероприятия:
- защита проектов на уровне территориальных дирекций и в Дирекции тяги;
- смотр-конкурс лучших по территориальным дирекциям проектов для участия в сетевом конкурсе;
- обучающий семинар руководителей структурных подразделений на полигоне наиболее опытной в данной работе Октябрьской дирекции тяги;
- научно-технический совет секции «Локомотивное хозяйство ОАО "РЖД”» по внедрению и тиражированию проектов «Бережливого производства», запланированный на июль 2013 г.
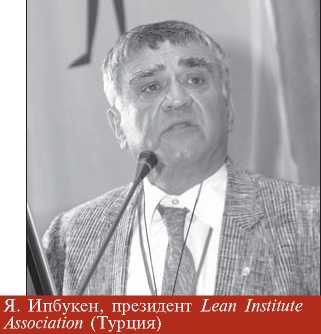
Рис. 2. Обучение и вовлечение персонала в процесс бережливого производства
Проекты обучения подразумевают:
- привлечение экспертов, прошедших обучение на специализированных курсах;
- эксперты, в свою очередь, обучают лидеров по территориальным дирекциям.
Лидеры из числа специалистов и руководителей территориальных дирекций выезжают на «линию» и подготавливают новаторов в структурных подразделениях, которые активно включаются в программу и обучают сотрудников данного структурного подразделения основным инструментам проекта «Бережливое производство» (рис. 2).
Программы обучения для каждого уровня разные. Цель одна — вовлечь в активную деятельность всех работников, повысить компетентность сотрудников в деле оптимизации процессов, повышения качества и эффективности работы. Принципы бережливого производства эффективны только тогда, когда используются массово, и каждый на своем рабочем месте думает, как улучшить технологический процесс. Поэтому в этом деле необходим комплексный подход с участием смежных служб.