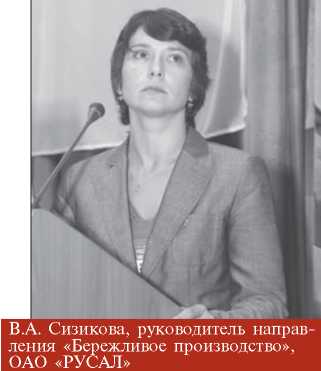
Рис. 1. Организация рабочего пространства по системе 5S в депо Петрозаводск
Для реализации программы были созданы рабочие группы как на уровне аппарата управления дирекции, так и в ремонтных локомотивных депо. Было обучено 17 специалистов (лин-экспертов), которые ежемесячно проводят обучение и делятся опытом не только с персоналом дирекции, но и осуществляют свою деятельность на всем полигоне Октябрьской дороги.
В соответствии с распоряжением старшего вице-президента В.А. Гапановича от 24.01.2012 № 102р перечень пилотных структурных подразделений по внедрению технологий бережливого производства охватывает все 12 ремонтных локомотивных депо дирекции.
В рамках реализации программы внедрения бережливого производства во всех ремонтных локомотивных депо отлажена система по разработке функциональных проектов улучшений, направленных на снижение основных видов потерь. Только за 2012 г. реализовано 38 проектов с общим экономическим эффектом около 17 млн. руб.
Одним из лучших в данном направлении работы является ремонтное депо Петрозаводск, где с 2010 г. реализуются методики бережливого производства. В настоящее время коллективом достигнуты ощутимые результаты, накоплен опыт, который может быть с успехом применен и на других предприятиях.
Такие основополагающие принципы стандартов ИСО, как «постоянное улучшение» и «вовлеченность персонала» осуществляются за счет реализации программы по развитию производственной системы предприятия. Указанная программа позволит достичь поставленных целей по снижению непроизводительных потерь, снижению времени цикла основных производственных процессов и повышению производительности труда.
По результатам формирования макрокарты производства основных сквозных процессов были выявлены ключевые проблемы, определены главные направления работы, установлены цели и показатели эффективности предлагаемых решений. При этом фундаментом стало становление новой системы производства с тремя развивающимися основами:
- развитие людей, что позволит создать условия для формирования и роста внутренней мотивации, уменьшить время, потраченное персоналом в производственных процессах, и тем самым снизить негативное воздействие производства, а также сохранить физическое и эмоциональное здоровье;
- развитие процессов, при помощи которых возможно снизить время производственного цикла, сократить производственные потери, обеспечив баланс производства;
- развитие менеджмента, способствующего формированию эффективной системы управления предыдущими основами.
Первостепенным методом реализации улучшений производственных процессов в ремонтном депо является применение принципа «малых групп». Использование данного принципа сводится к тому, что снижением непроизводительных потерь и увеличением эффективности выбранного производственного процесса занимается немногочисленная рабочая группа. Она состоит из лидера, привлекаемых специалистов и рабочих, разбирающихся в избранном производственном процессе.
В 2012 г. результатом работы «малых» групп стали разработка и успешная реализация десяти функциональных проектов улучшения производственных процессов с общим экономическим эффектом более 6 млн. руб. Так, осуществление проекта по сокращению времени простоя локомотива в ремонте позволила сократить время цикла ремонта в объеме ТР-3 локомотивов серии ТЭМ2 и ЧМЭЗ благодаря переносу позиции выкатки тепловоза на 40 %.
По результатам повторного картирования было зафиксировано снижение времени цикла выполнения ремонта за счет снижения непроизводительных потерь, связанных с ожиданием освобождения ремонтной позиции. Кроме того, из-за расположения выкатной позиции в основном цехе были созданы условия для использования переходного запаса экипажной части и дизель-генераторной установки, что, в свою очередь, позволит еще более уменьшить время цикла ремонта локомотива.
Для снижения времени ремонта вспомогательного оборудования, дизеля и автотормозного оборудования были изменены планировочные решения ремонтных участков, изготовлена необходимая технологическая оснастка и приведены рабочие места в соответствие с требованиями системы организации рабочего пространства 5S (рис. 1). Кроме того, сделан первый шаг к реализации вытягивающего принципа системы ремонта агрегатов дизеля посредством формирования доски заказов Канбан («точно в срок»).
Реализация поставленных задач функциональных проектов, в свою очередь, позволила по сравнению с 2011 г. достигнуть стратегических целей, предусмотренных программой внедрения бережливого производства в депо в 2012 г., а именно:
- время простоя локомотива в ремонте снижено в среднем на 15 %;
- производительность труда увеличена на 21,4%;
- величина нормативных запасов уменьшена на 19%;
- себестоимость приведенной единицы ремонта снижена на 23 %.
Выбранное направление развития производственной системы стало залогом успешного участия депо в конкурсе на Кубок лидеров производительности имени А.К. Гастева. С июля 2012 г. экспертные группы по 3 человека проводили аудиты производственных систем предприятий-конкурсантов по специально разработанному регламенту оценки.
На каждую компанию было отведено 2 дня. За это время эксперты наблюдали производственные и управленческие процессы, знакомились с документацией, опрашивали персонал. После этого подводили итоги и выдавали руководству принимающих предприятий рекомендации по совершенствованию производственных систем.
Затем был выстроен балльный рейтинг. Полученные результаты утверждены Наблюдательным советом конкурса, в который входили лучшие отечественные производственные менеджеры и эксперты-консультанты по качеству, бережливому производству и развитию производственных систем, а также автор бестселлера «Dao Toyota. 14 принципов менеджмента ведущей компании мира», президент консалтинговых компаний «Liker Lean Advisors» и «Академия Dao Toyota» Джеффри Лайкер.
В итоге депо Петрозаводск по результатам конкурса заняло почетное 3-е место среди предприятий России и стран СНГ.