Эффективность работы предприятия складывается из множества факторов: эффективности процессов, персонала, оборудования. Простои, снижение скорости, необходимость ремонта и переналадки непосредственным образом влияют на прибыль предприятия. Одной из современных методик, позволяющих минимизировать негативное влияние этих факторов, является инструмент бережливого производства - система TPM.
TPM (Total Productive Maintenance - всеобщее обслуживание оборудования) - это один из инструментов бережливого производства, применение которого позволяет снизить потери, связанные с простоями оборудования из-за поломок [1].
Основные аспекты TPM:
- повышение производительности и срока службы оборудования за счет более качественного ухода и внимательного отношения к требованиям по эксплуатации;
- повышение производительности и качества обслуживания оборудования за счет обучения и повышения мотивации рабочих;
- коллективное выявление причин неисправностей, поиск возможностей повышения производительности за счет перепланировки рабочих помещений, изменения операций по переналадке [2].
Основное отличие TPM от других концепций состоит в вовлечении операторов в процесс технического обслуживания оборудования. Отказ от подхода: «Я - оператор, значит, работаю, вы - ремонтная бригада, значит ремонтируете».
Как правило, решение о внедрении тех или иных инструментов исходит от руководства, и здесь самое главное было создать необходимую информационную поддержку на всех уровнях, через которые простым и понятным языком доносится информация о предстоящих изменениях с описанием этапов реализации изменений, указанием подразделений, кого коснутся изменения, и их роли, а также выгод для работников соответствующих подразделений и компании в целом. Конечной целью информационной поддержки было сформировано понимание работников о том, что изменения необходимы и неизбежны.
На этапе информационной поддержки было описано текущее состояние и этапы преобразования, а также составлен план-график реализации проекта.
До начала внедрения проекта были обнаружены следующие проблемы:
- не проверялось состояние оборудования перед запуском;
- недостоверная информация об остановках производства;
- слабый фокус системы на предупредительных ремонтах;
- недостаток персонала в дежурной службе;
- технический персонал узко специализирован;
- отсутствует согласованность внутри ТО;
- слабо развита система поиска первопричин поломок.
Повышение эффективности инженерной службы осуществлялось в шесть этапов, где с третьего по пятый этапы шли параллельно:
- система обходов осмотров;
- изменение системы учета простоев;
- создание и внедрение системы ППР;
- обучение базовым ремонтам;
- реорганизация ТО;
- постоянное совершенствование системы [3].
Следующим шагом по внедрению системы TPM стало разграничение зон ответственности подразделений и обозначение роли каждого участника. С самого начала реализации проекта главной целью было максимальное вовлечение работников соответствующих подразделений и формирование из них межфункциональной команды для разработки стандартов осмотра и обхода оборудования, регламентов взаимодействия между службами. В нее входили -специалист проекта ТРМ, мастер участка, лучший оператор, главный механик, слесарь инженерной службы и технолог, при необходимости также привлекался электрик. Привлекая работников из разных подразделений в совместную деятельность, удалось наладить конструктивное взаимодействие между подразделениями на базовом уровне.
Результатом работы межфункциональной команды является разработанная и согласованная Система постоянной диагностики оборудования, которая включает в себя алгоритм взаимодействия между службами, стандарт обхода оборудования слесарем и визуальную поддержку в виде доски обхода представленные на рис. 1, 2 и 3 соответственно.
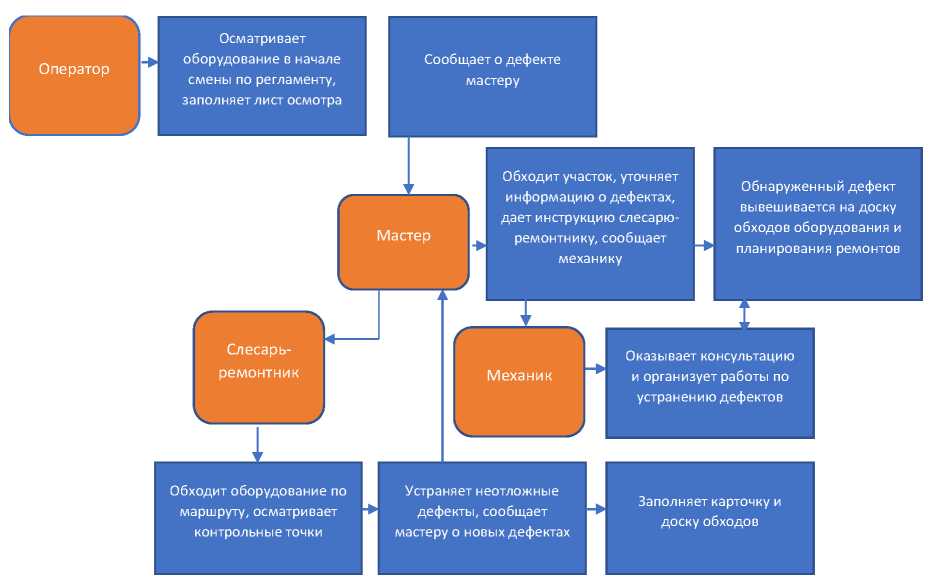
Рис. 1. Алгоритм взаимодействия между службами
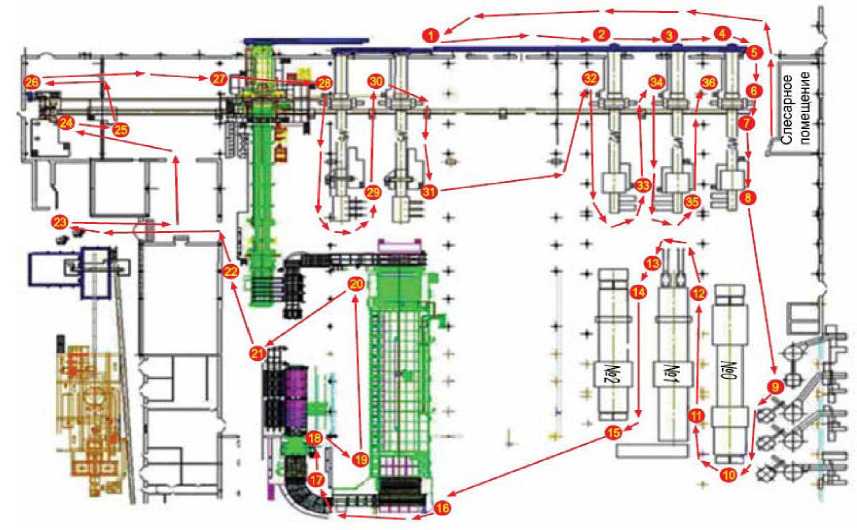
Рис. 2. Визуализация маршрута обхода оборудования слесарем
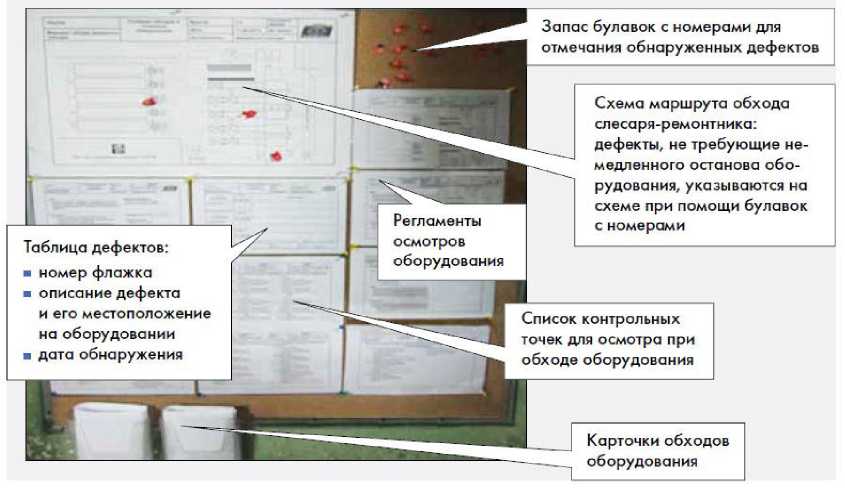
Рис. 3. Пример визуальной поддержки: «Доска обходов оборудования слесарем», размещенная для инженерной службы
До внедрения проекта на предприятии фиксация и учет простоев велся в свободной форме, «кто как умеет», без четкой классификации. Сотрудники производственного отдела и инженерной службы фиксировали в своих формах, а по итогам месяца перекладывали вину друг на друга за часы простоев .Поэтому необходимо было разработать систему учета простоев с необходимой детализацией, простой, понятной, что в дальнейшем позволит проводить анализ и поиск первопричин простоев. Этап разработки и внедрения системы учета простоев был начат параллельно с разработкой необходимых нормативных документов.
Разработанная система учета простоев в рамках внедрения проекта системы TQM включала в себя:
- бланк регистрации простоев, где фиксировалось время остановок и ремонта, определялась группа простоя и указывалась причина простоя и действия по его устранению;
- каскад звонков - последовательное информирование о поломке, эскалация проблемы с четко определенными временными рамками;
- картографию линии - документ, позволяющий определить приоритет поломки, правильно скоординировать технический персонал.
Система учета простоев также служит для построения показателей надежности оборудования, что в свою очередь является ключевым показателем эффективности (КПЭ) работы инженерной службы, представленный на рис. 4.
Индикаторы надежности
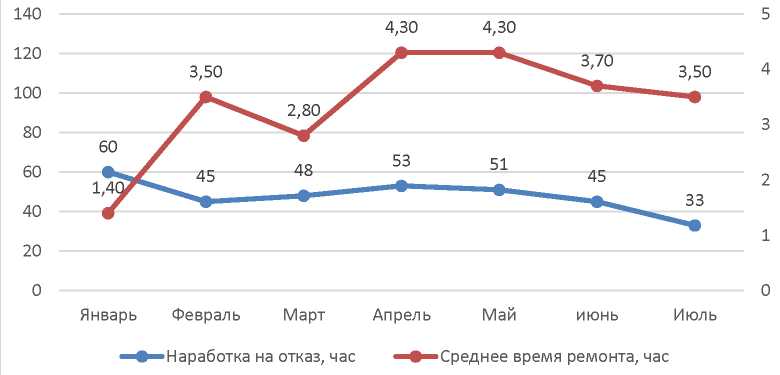
Рис. 4. Показатели надежности оборудования за период с января по июль 2019 года на промышленном предприятии
Одним из самых длительных и трудоемких этапов являлась разработка нарядов планово предупредительных ремонтов (ППР). В первую очередь наряды ППР разрабатывались на оборудование, которое являлось узким местом с точки зрения производительности.
На этапе построения системы управления запасными частями определился необходимый уровень запасов запчастей, была разработана номенклатура и правила управления запасными частями.Но сам по себе учет простоев не повлек за собой их сокращение, поэтому следующим этапом стала система анализа и поиска первопричин простоев. Особое внимание на данном этапе уделялось обучению инженерно-технических работников (ИТР): методам краткосрочного и среднесрочного планирования; методам анализа простоев и поиску первопричин неисправности.
При внедрении проекта ТРМ изменилась организационная структура технической службы. Суть изменений заключалась в выделении инженерного блока и формировании дежурной службы в составе слесаря, электрика, электронщика и начальника. Функция инженерного блока - это еженедельный анализ показателей надежности оборудования, анализ длительных простоев, корректировка карт и плана ППР, контроль качества выполнения ППР, участие в устранении сложных поломок, разработка корректирующих мероприятий, отслеживание и комплектация склада запчастей.
Таким образом, разработанная и внедренная система ТРМ на промышленном предприятии стала эффективным решением проблем, препятствующих постоянному совершенствованию системы менеджмента качества.
Волгоградский государственный технический университет ООО «ПО «Аквамаш»
БИБЛИОГРАФИЧЕСКИЙ СПИСОК
- Система ТРМ (англ.) - более четверти века в России. Японская теория. Российская практика. Опыт Консультационного сообщества «ТАИР» / Т. М. Куприянова, В. Е. Растимешин. - М. : ООО «Буки Веди», 2019. - 644 с.
- Вэйдер, М. Инструменты Бережливого производства: минируководство по внедрению методик Бережливого производства : пер. с англ. / М. Вэйдер. - М. : Альпина Бизнес Букс, 2015. - 125 с.
- Пшенникова, М. В. Система ТРМ: хроника внедрения / М. В. Пшенникова // Методы менеджмента качества. - 2015, № 10. - С. 18-19.