Теория ограничений (ТОС, Theory of constraints) - популярная концепция менеджмента, разработанная в 1980-х гг. доктором Элией Голдраттом. Она предлагает концентрировать организационные ресурсы на устранении ограничений (конфликтов), которые мешают компании полностью реализовать ее потенциал. Метод рассуждений Голдратта составляет основу теории ограничений и позволяет успешно разрешать множество противоречий: межу сроками и качеством, стоимостью и затратами, требуемой производительностью и имеющимися ресурсами [1].
Некоторые последователи ТОС считают, что успешное применение теории ограничений имеет тенденцию к увеличению производственных мощностей. На наш взгляд, этот подход демонстрирует очень узкое понимание теории ограничений. Находясь в данной предсубпозиции, целесообразнее считать, что теория ограничений направлена на преодоление ограничений, связанных с ошибочными убеждениями менеджмента. Такие убеждения часто приводят к потере системой возможности достижения больших результатов, а также, в частности, к ограничению скорости потока. На наш взгляд, в основе ТОС лежит принцип - улучшение потока, а «роль профессионального менеджера заключается в постоянном улучшении деятельности системы, за которую он отвечает» [2, стр. 2].
Исследователи, имеющие опыт внедрения положений ТОС на практике, сталкиваются с необходимостью сравнения преимуществ и недостатков применения теории ограничений по сравнению с бережливым производством (Lean Production).
Бережливое производство и теория ограничений являются системными методами повышения эффективности производства. Однако они имеют достаточно разные подходы. Теория ограничений сосредоточена на выявлении и устранении ограничений потока, которые сдерживают пропускную способность потока. Бережливое производство сосредоточено на ликвидации потерь производственного процесса.
Ошибочным представляется мнение, что бережливое производство ведет к сокращению производственных затрат, так как оно сосредоточено на ликвидации потерь производственного процесса. На наш взгляд, в основе Lean лежит тот же принцип, что и в основе ТОС - улучшение потока. Достигается это через сокращение незавершенного производства, что в свою очередь достигается через принцип вытягивания и сокращение количества деталей в передаточной партии. Необходимость сокращения потерь в бережливом производстве возникает только в результате необходимости отладки потока [3].
Рассмотрим более подробно механизмы поддержания потока, используемые соответственно в теории ограничений и в рамках бережливого производства.
На рисунке показано, как пять фокусирующих шагов по теории ограничений могут использовать инструменты бережливого производства. Рассмотрим основные инструменты бережливого производства, которые могут быть использованы на каждом из пяти фокусирующих шагов в концепции теории ограничений по мнению В. Речкалова [3].
Value Stream Mapping (VSM) - карты создания потока ценности - визуально отображают по-ток производства (текущее и будущее состояния) с помощью определенного набора символов и приемов. Карты обеспечивают основу для дальнейшей работы при определении ограничения. Например, время цикла для каждого этапа может быть отмечено на карте. VSM вовлекают команды сотрудников и полезны для решения проблем, а также для документирования сложных процессов.
Value Stream Mapping (VSM) - карты создания потока ценности - визуально отображают поток производства (текущее и будущее состояния) с помощью определенного набора символов и приемов. Карты обеспечивают основу для дальнейшей работы при определении ограничения. Например, время цикла для каждого этапа может быть отмечено на карте. VSM вовлекают команды сотрудников и полезны для решения проблем, а также для документирования сложных процессов.
Gemba призывает выходить из офиса и проводить время в цехах завода, что способствует глубокому и полному пониманию реальных проблем производства - наблюдения из первых рук и разговоры с рядовыми работниками завода. Прогулки по цеху, наблюдение за производством и взаимодействие с работниками может быть очень эффективным способом сбора информации, которая помогает определить ограничения.
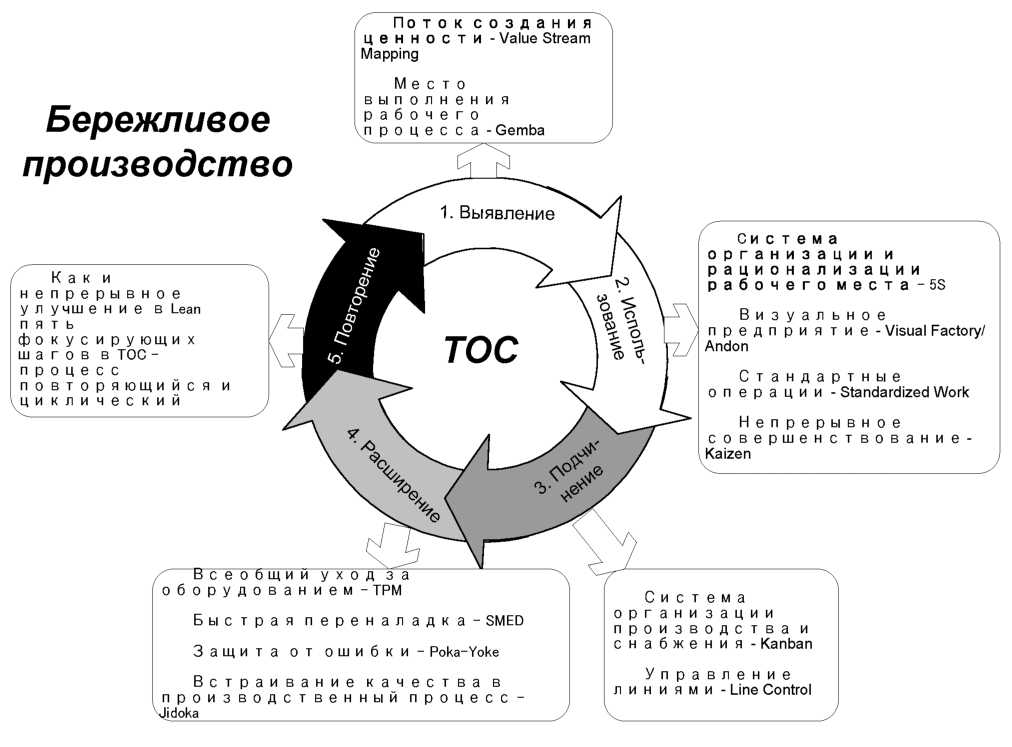
Основные инструменты бережливого производства на каждом из пяти фокусирующих шагов в концепции теории ограничений [3] 5S представляет собой программу для устранения потерь, которые являются результатом плохо организованного рабочего места. Система 5S создает основу для лучшей производительности на ограничении, позволяет быстрее выявлять возникающие проблемы в ограничении, а также приводит к повышению мотивации и гордости сотрудников (в результате улучшения условий работы).
Visual Factory / Andon представляет собой стратегию передачи информации через легко видимые визуальные образы. Доски или визуальные дисплеи Andon показывают статус процессов и позволяют привлечь немедленное внимание операторов к проблемам. Таким образом, можно немедленно приступить к их решению.
Standardized Work представляет собой сохранение наиболее успешного опыта сотрудников в документах, которые последовательно применяют все операторы и которые сохраняются до следующего улучшения. Таким образом, стандартные операции увеличивают производительность за счет последовательного применения передового опыта работы с ограничением, уменьшают количество вариаций путем применения стандартизированных процедур в работе с ограничением, а также гарантируют, что все операторы будут действовать одинаково и наилучшим образом.
Kaizen обеспечивает основу для работы сотрудников в небольших группах, которые предлагают и осуществляют постепенные улучшения в производственном процессе. Kaizen накапливает в себе коллективный талант компании, чтобы создать двигатель для непрерывного совершенствования, обеспечивает проверенный механизм генерации идей о том, как использовать ограничение, определяет возможности «быстрой победы» для повышения пропускной способности ограничения, а также вовлекает операторов работать в команде и критически относиться к своей работе.
Kanban предлагает простые визуальные методы для регулирования потока материалов/деталей, синхронизирует использование материалов ограничением с использованием материалов на более ранних стадиях процесса, путем сигнала, когда новые материалы нужно запускать в процесс.
Line Control представляет собой сложный метод, используемый совместно с синхронными автоматизированными линиями, такими как линии по производству FMCG (товаров повседневного спроса). Метод подчиняет не являющееся ограничением оборудование ограничению таким образом, чтобы увеличить общую производительность системы. Таким образом, Line Control обеспечивает альтернативу традиционному инструменту DBR (Drum-Buffer-Rope, «барабан-буфер-канат») для FMCG линий, оптимизирует скорости работы ограничений и не-ограничений для максимальной пропускной способности и снижения количества незначительных остановок, уменьшает задержки запуска деталей в ограничение путем синхронизации запуска оборудования.
TPM уменьшает частоту поломок оборудования на ограничении и количество незначительных остановок, предоставляет операторам более сильное чувство «собственности» на их оборудование, позволяет планировать и производить обслуживание оборудования в основном в непроизводственное время, нацеливает на решение проблем с качеством путем поиска и удаления корневых причин дефектов.
SMED значительно сокращает время переналадки на ограничении. SMED увеличивает время полезной работы ограничения, позволяет чаще менять настройки и уменьшать размер партий, что приводит к улучшению скорости реакции на потребительский спрос, обеспечивает более гладкий запуск новой продукции, так как упрощенные и стандартизированные процессы переналадки улучшают качество и стабильность выхода продукции.
Poka-Yoke используется для обнаружения дефектов и предотвращения их возникновения в оборудовании с целью достижения нулевого количества дефектов. Например, разъем проектируют ассиметричным, чтобы его невозможно было соединить с неправильной полярностью. Poka-Yoke уменьшает количество дефектов (что также очень важно после ограничения), позволяет увеличить время автономного обслуживания.
Jidoka означает «интеллектуальная автоматизация» или «человекоавтоматизация». Частичная автоматизация значительно дешевле, чем полная автоматизация. Jidoka также использует автоматическую остановку оборудования при обнаружении дефектов. В некоторых случаях ограничение не может быть преодолено без значительных капитальных вложений.
Jidoka может дать ценные указания по проектированию оборудования и его модернизации.
Таким образом, бережливое производство имеет отличный инструмент для визуального отображения потоков продукции (карты потока создания ценности, Value Stream Mapping), а также философию, которая призывает проводить достаточно времени и принимать решения непосредственно на месте производственного процесса (Gemba). Бережливое производство решительно поддерживает идею сделать все, что в ваших силах, что также является основной темой для использования ограничений. Например, бережливое производство учит организовать рабочую зону (5S), мотивировать и расширять права и возможности работников (Visual Factory / Andon), использовать лучшие практики (Standardized Work), использовать мозговой штурм для поиска идей по дополнительному улучшению (Kaizen). Производственные методики Lean для регулирования потока (Kanban) и синхронизации автоматизированных линий (Line Control) могут быть применены для подчинения и синхронизации работы всего производства с ограничением. Производственные методы Lean: всеобщее обслуживание оборудования (TPM); значительное сокращение времени переналадки (SMED); обнаружение дефектов и профилактика их возникновения в производственных процессах и оборудовании (Poka-Yoke); частичная автоматизация/интеллектуализация оборудования (Jidoka) — оказывают непосредственное воздействие на улучшение ограничения. TPM и SMED могут также рассматриваться как методы эксплуатации техники для обеспечения максимальной пропускной способности, используя только имеющиеся в настоящее время ресурсы.
Рассмотрим, почему в части механизма поддержания потока теория ограничений и бережливое производство в корне отличаются друг от друга, и их соответствующие механизмы - «барабан-буфер-канат» (DBR) и Kanban не могут быть совмещены [3].
Kanban уменьшает незавершенное производство путем ограничения и постепенного сокращения количества контейнеров и деталей в них, вытягиваемых последующей операцией из предыдущей. DBR же ограничивает незавершенное производство совсем другим путем - фиксируя время, в течение которого заказ находится в производстве (время буфера). Буфер выбирается исходя из того, чтобы ресурс с ограниченной мощностью не простаивал и незавершенное производство сокращалось. Буфер защищает ресурс с ограниченной мощностью от простоя. Приоритеты в обработке заказов устанавливаются на основе статуса буфера - времени, оставшимся до конца обработки заказа. Поэтому Kanban для управления на основе теории ограничений использовать нецелесообразно. Передача деталей в условиях Lean происходит одновременно между всеми операциями, на основе времени такта. В условиях бережливого производства возможны ситуации, когда одна из операций не смогла выполнить свой объем работ за время такта (поломка, ошибка, брак и т.д.). В этом случае используется механизм Andon для остановки всей линии и решения проблемы. В условиях теории ограничений такая ситуация невозможна, так как операции разъединены между собой за счет механизма буфера. Поэтому механизм Andon в условиях теории ограничений также применять нецелесообразно. Аналогичная ситуация наблюдается и с применением принципов Jidoka.
Подводя итог, следует сказать, что, на наш взгляд, ТОС и Lean не противоречат, а дополняют друг друга. Проблема взаимосвязанного применения этих двух концепций носит ситуативный характер и может быть описана так: многие компании, не понимая системности ТОС, применяют методы бережливого производства в то время, когда менеджменту стоит обратить внимание на теорию ограничений. Иными словами, если в компании не выстроены бизнес-процессы, нет стратегии развития, отсутствует долгосрочное планирование, а сотрудники не знают, чего от них ждет руководство, то Lean заранее обречено на провал. ТОС же позволяет взглянуть на всю цепочку создания ценности сверху, определить в ней узкое место и направить туда ограниченные ресурсы. Однако в то же время есть недостаток и в применении теории ограничений. Исследователи ТОС говорят, что проблемы нужно решать по мере их поступления, однако, когда появляется узкое место на каком-то участке для того, чтобы его расшить, требуются серьезные ресурсы и длительное время. Из этого следует, что для успешного функционирования менеджмент предприятия должен до конца осознать преимущества применения TOC и Lean, а также разницу между бережливым производством и теорией ограничений.
Литература
- Детмер У. Теория ограничений Голдратта: Системный подход к непрерывному совершенствованию / Уильям Детмер; Пер. с англ. - 2-е изд. - М.: Альпина БизнесБукс, 2008. - 444 с.
- Коуэн О. Основы Теории Ограничений / Одед Коуэн, Елена Федурко; Пер. Д. Абросимова. TOC Strategic Solutions. Tallinn. Estonia. 2012. 331 с.
- Речкалов В. Интеграция Бережливого производства и Теории Ограничений. Электрон.дан. Режим доступа: http://www.tocpeople.com/2012/09/berezhlivoe-proizvodstvo-toc/#comment-600