По оценке экспертов, нынешняя ситуация по развитию и внедрению бережливого производства (Lean) на российских предприятиях отличается следующими характерными чертами:
- слепое копирование принципов и инструментов, заимствованных у продвинутых зарубежных компаний;
- отсутствие людей, способных создавать бережливое производство;
- отсутствие системы внедрения бережливого производства.
По моему мнению, эти проблемы взаимосвязаны, и их решение сопряжено с изучением собственного производства через развитие способности персонала «видеть» процессы.
Попробуем разобраться с первым пунктом. Что можно скопировать? Простейшие приемы и методы. Ознакомиться с принципами 5S, навести поверхностный блеск на участках и рабочих местах, провести кампанию по внедрению точечных кайдзенов (или кайдзенов процесса — улучшения, которые осуществляются точечно, на отдельных рабочих местах), снизить трудоемкость, оформить бригадные доски. На этом процесс внедрения бережливого производства начинается и, увы, часто и заканчивается. При подведении итогов оказывается, что результат не оправдал ожиданий, вложенные деньги не окупились. В лучшем случае, повысилась культура и внешняя привлекательность производства. Руководство разочаровано, персонал ничего не понял. Застой в развитии приводит к откату с завоеванных позиций. С приходом нового «гуру», как правило, приглашенного со стороны, все повторяется.
Есть ли более мощные методы и инструменты в наборе бережливого производства, позволяющие сделать прорыв с точки зрения повышения эффективности производства? Да, есть. Например, управление потоками создания ценностей. Подтверждение тому — оценка соотношения эффективности кайдзена потока (совершенствование потока создания ценностей) и точечного кайдзена с позиции Lean. При всем уважении к точечному кайдзену, необходимо признать, что кайдзен потока — это прорыв в организации производства, позволяющий иногда многократно повысить его эффективность.
Можно ли заимствовать подобные более сложные методы и инструменты? В целом и напрямую, по-моему, нельзя.
Во-первых, Lean-инструменты необходимо адаптировать к условиям собственного производства и провести довольно большую самостоятельную работу по выстраиванию потоков.
Во-вторых, подобный опыт позаимствовать негде. В руководствах по бережливому производству содержатся очень скупые сведения по управлению потоками создания ценностей, а тем более — по методологии выстраивания данных схем управления. Сделано ли это случайно или преднамеренно? Второе не исключается.
Известно, что первые опыты внедрения системы канбан и принципов работы по системе супермаркета в компании Toyota не были успешными, пока не был внедрен поток единичных изделий и не произведено его выравнивание (хейд-зунка). Иными словами, прямое копирование увиденного в супермаркете без понимания собственных процессов и взаимной адаптации к условиям производства не принесло успеха. Может быть, основоположник Производственной системы Toyota (TPS) Тайичи Оно долгое время не хотел рассказывать о системе канбан и принципах управления потоком создания ценностей потому, что этому невозможно научить заочно? K этому необходимо прийти через видение процессов с использованием собственных знаний с позиций принципов бережливого производства.
Так что же надо знать и уметь, чтобы перерасти стадию слепого копирования? Нужно уметь видеть процессы. И не просто видеть, а рассмотреть через призму собственных знаний, которые могли бы помочь увидеть то, что не заметили другие. А знания, в свою очередь, должны помочь сделать то, что другие не могут сделать. Сделать нешаблонно, нестандартно и максимально эффективно. Для этого знание необходимо максимально приблизить к рабочим центрам. Знание состоит из понимания процесса, выделения и постановки задачи для решения и способности ее решить.
Каковы же сильные стороны Производственной системы Toyota? Создала ли она новые принципы управления? На мой взгляд, нет, тем более что история промышленного производства намного старше фирмы. В TPS собраны, аккумулированы и развиты принципы управления производством, разработанные и применяемые по всему миру. Дисциплинированность и мотивация персонала позволили обеспечить стабилизацию нововведений и постоянное совершенствование процессов развития.
Любое промышленное производство, любой завод в любом уголке мира, поставив подобные цели, может прийти к абсолютно идентичной системе. Это обусловлено идентичными законами развития производства. Развитие собственных процессов является реальной эффективной альтернативой слепому копированию чужих бригадных досок.
Мы проделали работу по управлению потоками производства изделий на ОАО «Ульяновский автомобильный завод» (далее — УАЗ), не имея информации о потоке единичных изделий, применяемом в компании Toyota. Были созданы: система учета простоев конвейеров (функционирующая по принципу анализа времени такта линии) и автоматизированная система планирования и контроля очередности прохождения потока единичных изделий по цехам завода (так называемая жесткая закладка). При этом подход осуществлялся исходя из российского опыта организации производства и существующей планировки завода. Было интересно найти позже в описании TPS подобные приемы и подходы. Это подтверждает идентичность методов и принципов управления производством в российской практике и за рубежом.
На отечественных предприятиях сборкой автомобилей всегда управляли при помощи «закладки» (последовательность сборки изделий), на зарубежных — применяется поток единичных изделий, или SILS (Supply in Line Sequence). За рубежом в качестве инструмента отслеживания используют takt-time, у нас планирование и расстановка персонала по линиям производится с сопоставлением времени такта. Руководства по Lean могут помочь в разработке производственной системы и ускорить ее формирование, но прежде необходимо те же самые процессы увидеть у себя. После этого вполне самостоятельно можно создать не менее эффективные инструменты на собственном производстве.
Что необходимо для этого? Подготовленный персонал, начиная с команды перемен, которая соответствовала бы вышеуказанным требованиям. Агент перемен, способный направлять перемены и контролировать их пульс, способный развивать, а не подменять команду перемен. Естественно, поддержка руководства.
Такие же требования можно предъявить к человеку — организатору внедрения концепции Lean?
Должен ли он быть практиком?
Да.
Должен ли он быть теоретиком?
Да.
Важнейший принцип бережливого производства — построение потоков создания ценностей.
В определенной степени он должен быть одновременно и тем и другим. Иными словами, он должен быть аналитиком — человеком, способным успешно сочетать и применять как теоретические знания, так и практические. Находить информацию, анализировать и систематизировать ее, разрабатывать и внедрять оригинальные решения.
Самый верный способ собрать команду таких людей — вырастить их. Только данный способ гарантирует последовательное улучшение процессов. Покупкой стороннего «гуру» данный вопрос не решить. Однако и отбор собственных специалистов должен быть очень критичным, и кандидаты не должны отбираться по остаточному принципу — кто не подошел другим отделам.
Значимая роль в процессах управления производством, особенно при многономенклатурном и высокотехнологичном производстве, отводится компьютерным технологиям. С их помощью более эффективно решаются вопросы по сбору данных, их систематизации и анализу, разработке новых задач. Специалист, обладающий данными знаниями, может находить самые оригинальные и действенные решения, недоступные другим. В то же время программист без знания процессов производства не сможет найти применения своим способностям, для этого необходимо либо работать непосредственно в производстве, либо иметь квалифицированного постановщика — заказчика задач.
В последнее время можно часто встретить обсуждение путей развития управления производством (процессами): глобальная автоматизация или внедрение принципов бережливого производства. Очевидно, что противопоставлений быть не должно, и необходимо находить золотую середину. Мощнейшая информационная система может не оправдать себя с точки зрения эффективности управления производством, если не применять принципы Lean. В то же время бережливое производство становится мощнее с использованием возможностей компьютерных технологий. Торжествует принцип: автоматизации должно быть ровно столько, сколько необходимо. При этом первейшая роль отводится постановке задачи. Прежде чем внедрять информационную систему, необходимо понять, что же она даст.
При постановке задач по управлению потоками на ОАО «УАЗ» мы руководствовались, в первую очередь, их необходимостью и соответствием оптимальным схемам управления. Это задачи по управлению процессами с использованием средств автоматизации, но автоматизация не была самоцелью. Другими словами, были исследованы процессы, сформированы принципы управления ими, и разработанные схемы опробованы в первоначальном варианте в ручном режиме. Разработка и внедрение программного сопровождения обеспечило реализацию данных задач и придало им мощный статус.
Организатор внедрения концепции Lean должен быть аналитиком — человеком, способным успешно сочетать и применять как теоретические знания, так и практические. Находить информацию, анализировать и систематизировать ее, разрабатывать и внедрять оригинальные решения.
И, наконец, создание системы внедрения бережливого производства. Важнейший принцип бережливого производства — построение потоков создания ценностей. Сумейте выстроить потоки, оценить их эффективность, выявить проблемы и найти способы их решения — и получите мощную платформу для построения бережливого производства.
Внедрение автоматизированной системы учета простоев конвейеров в рамках проекта «Производственная система ОАО «УАЗ»1
Одним из показателей эффективности организации производства является величина простоев производственных участков. Казалось бы простейший вопрос — выявление и снижение времени простоев — требует достаточно серьезного обоснования и отношения. Существует множество подходов к определению времени простоя в зависимости от поставленных задач, интересов исполнителей и конструкций конвейеров. Самым универсальным и простым методом является контроль такта конвейера. Как советуют идеологи бережливого производства: «...считайте такт», и они правы. Еще более эффективно, если такт считается, и вся необходимая информация обрабатывается автоматизированной системой, которая позволяет специалистам принимать решения и воздействовать на ситуацию. При применении автоматизации и современных технологий сбора информации появляется возможность определять время наступления каждого простоя с точностью до секунд и хранить всю информацию в базе данных.
В 2004 г. на ОАО «УАЗ», при двухсменной работе, простои составляли на сборочных конвейерах автомобилей около 2,5 ч в сутки для каждого. При этом практически отсутствовала информация о времени, причинах и виновниках простоев. По сути был узаконен принцип «план выполнен — значит, простоев не было». Подобный подход к проблеме приводил к неритмичной работе, неравномерной загрузке персонала, некомплектной и некачественной сборке и излишним затратам на производство автомобилей.
Уровень суточных простоев главных конвейеров за период октябрь 2004 г. -октябрь 2005 г., час
Не работал механизм хозрасчетных претензий к виновникам простоев, следовательно, отсутствовала ответственность участников процесса.
Для решения данной проблемы группой специалистов Дирекции по персоналу и Дирекции по информационным системам был организован пилотный проект по созданию и внедрению автоматизированной системы учета простоев (ритмичность работы) конвейеров и поточных линий.
Динамика простоев за август — октябрь 2005 г. по Управлениям и Дирекциям-виновникам, час
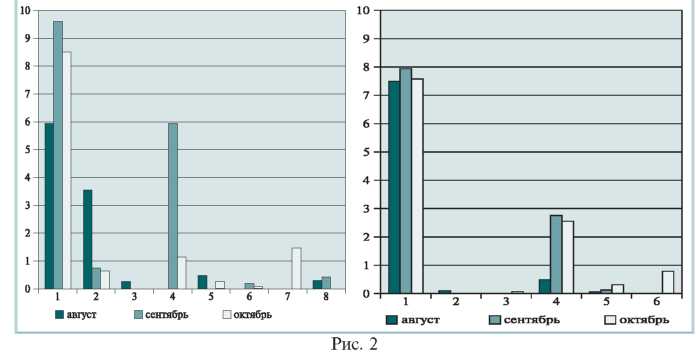
В итоге, в августе 2004 г. руководители завода и подразделений получили эффективный инструмент контроля и управления ходом производства. Простота системы позволила обойтись без каких-либо дополнительных материальных затрат. Универсальность системы позволила снимать показания как на постоянно движущихся конвейерах, так и на поточных линиях пульсирующего типа. В принципе, данную систему легко адаптировать к любым условиям производства и поставки комплектующих, графиков движения транспорта и т. д.
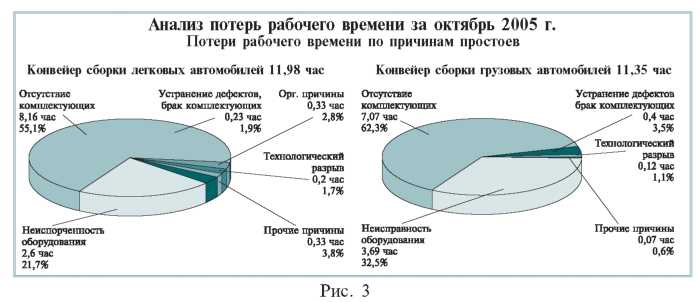
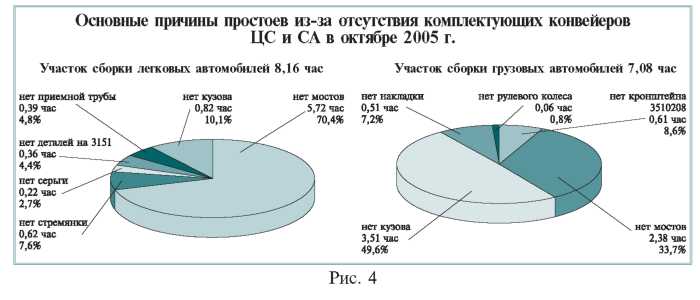
С момента внедрения автоматизированной системы тема простоев стала «горячей» на заводе. Ежедневно оперативно рассматривались вопросы по простоям главных конвейеров начальниками цехов, производственных участков и главным диспетчером. По итогам месяца материал рассматривался на совещании у генерального директора с участием руководителей завода. Подвергся корректировке и реально заработал механизм предъявления хозрасчетных претензий. Персональная ответственность руководителей подразделений заставила их глубже вникать в вопросы организации производства.
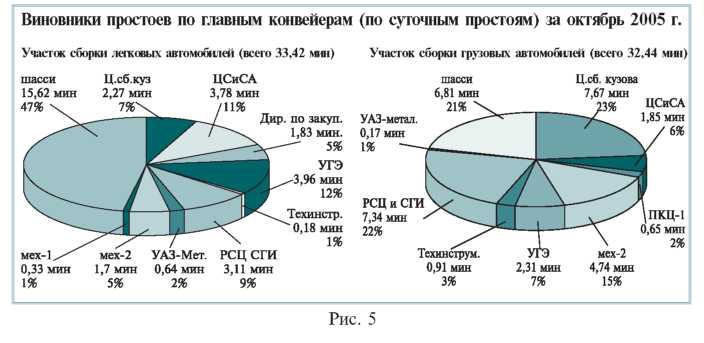
Методичная и последовательная работа привела к хорошему результату (рис. 1) — простои в среднем снизились на 77%!
Информация, собираемая системой, позволила получать отчеты:
- по виновникам простоев за конкретный месяц и в динамике за выбранный период (рис. 2);
- по причинам простоев (рис. 3);
- по детализации причин простоев (рис. 4);
- по виновникам простоев за месяц с указанием времени простоя (рис. 5);
- по величине хозрасчетных претензий за каждый простой и итоговым за месяц (рис. 6)
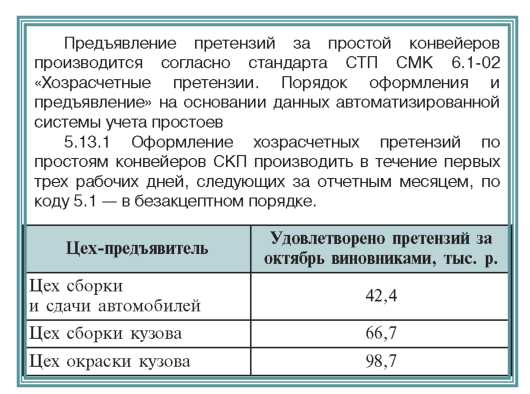
Рис. 6. Отчет по величине хозрасчетных претензий за простой конвейеров
После отработки проекта на главном конвейере, система стала распространяться по цехам сборки, окраски и сварки кузовов, механосборочным цехам, появились новые адреса в базе данных. Для развития данной системы был создан web-сайт в заводской системе, который дает подробную информацию со всех конвейеров завода по времени простоя, виновникам, причинам простоев и стоимости простоев. Доступ к сайту возможен с любого компьютера, подключенного к заводской сети, и каждый руководитель в любой момент времени может получать нужную информацию (рис. 7).
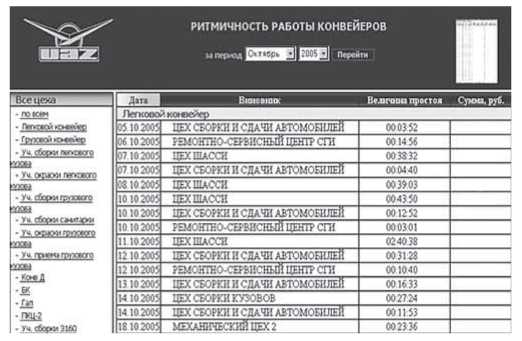
Итогом работы подразделений завода по снижению простоев с использованием системы стало снижение среднесуточных простоев главных конвейеров на 77%. Результат отразился на издержках производства, производительности труда и качестве выпускаемой продукции.
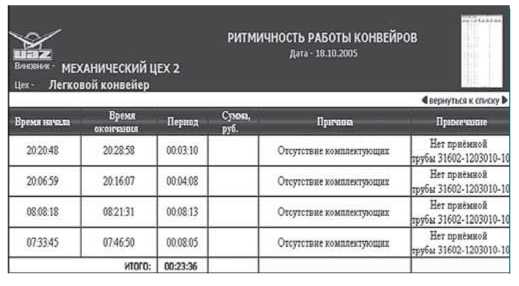
Рис. 7. Информация о ритмичности работы конвейеров
Устранение необоснованных потерь мощностей участков и рабочего времени персонала позволило перейти к более сложной работе по управлению потоками производства изделий — к производству изделий точно в срок на основе потока единичных изделий — «жесткой закладки».