Концепция бережливого производства в настоящее время становится одним из актуальнейших направлений менеджмента. В основе философии этой концепции - улучшение качества продукции с одновременным уменьшением затрат на производство за счет сокращения внутренних потерь. Эта цель достигается при помощи методов бережливого производства 5 S, «точно вовремя», канбан, «Poka Yoke», андон, ТРМ, и др.
Наибольшее распространение эти методы получили за рубежом, в частности, в автомобилестроении и машиностроении. В последние годы Российские машиностроительные и автомобилестроительные предприятия стали успешно внедрять методы бережливого производства.
В традиционном машиностроении, при котором изготавливаются отдельные узлы, агрегаты или детали, производство является дискретным, то есть отдельные операции по изготовлению и сборке изделия разнесены и разграничены во времени и пространстве.
В этих пространственных и временных промежутках, разграничивающих отдельные стадии производственной цепочки, происходят лишние непроизводительные действия, передвижение рабочих, перемещение материалов, создаются ненужные запасы деталей, потеря времени на поиск инструмента и деталей, что увеличивает время цикла создания ценности и повышает стоимость готового продукта.
Синхронизация поточного производства и применение принципов канбан и «точно в срок» и других методов бережливого производства позволяет избежать этих нежелательных явлений.
Синхронизированное поточное производство (СПП) может быть определено как «любой систематизированный подход, направленный на быстрое и плавное продвижение материалов через различные производственные ресурсы предприятия в гармонии с рыночными требованиями на его продукцию» [1].
такое производство может быть организовано как единичное поточное производство, состоящее из множества дискретных синхронизированных процессов, что делает его по существу непрерывным производством.
так, например, такое единичное поточное производство, осуществляемое как непрерывное производство, организовано на заводах Форда: «Мы начинаем производственный процесс с выплавки металла в доменной печи и завершаем его погрузкой собранных двигателей в грузовые вагоны. Отливки (блоков двигателей) в литейном цехе грузятся на подвижные платформы или на контейнеры, которые доставляют их на линию сборки, где их обрабатывают, дополняют всеми необходимыми деталями по мере продвижения на конвейере, и на выходе получают окончательно собранный и испытанный мотор. Все это происходит непрерывно, без единой остановки» [1].
таким образом, высокоорганизованное синхронизированное единичное поточное производство может быть сравнимо с непрерывным производством. В непрерывном производстве все материалы находятся в непрерывном движении, и отсутствует накопление их для последующей транспортировки. Такие производства изначально организуются на принципах «точно вовремя» и «канбан».
Классическим образцом непрерывного производства является химическое производство, возьмем, к примеру, предприятие N. В таких производствах газообразные, жидкие или твердые исходные материалы обрабатываются с применением различных физических, механических и химических процессов с целью получения востребованных продуктов.
Часто на химических производствах начальной стадией процесса является реактор, в котором осуществляется синтез, то есть целевое превращение исходных материалов в конечный продукт.
Как правило, получить в реакторе конечный продукт в чистом виде не удается. На выходе из реактора получается реакционная масса, состоящая из смеси целевого продукта, побочных продуктов, непрореагировавшего сырья.
В дальнейшем продукты синтеза перемещаются на другие участки производства, где подвергаются различным видам обработки, пока не будет получен конечный продукт. Такими видами обработки могут быть, например, термическая обработка, разделение по фракциям, очистка от примесей, фильтрация, кристаллизация, грануляция и т.п.
В таких химических процессах обрабатываемый материал движется непрерывным потоком от начала процесса до получения готового продукта и перемещения его на склад или непосредственно в транспортные средства для доставки заказчику.
Движение материалов осуществляется непрерывно в закрытых транспортных системах по всей производственной цепочке. Такими транспортными системами обычно являются насосы, компрессоры и трубопроводы. Перемещение материалов должно осуществляться безостановочно, так как при вынужденной остановке какого-либо звена в цепочке произойдет остановка всей производственной линии. Это отрицательно сказывается на процессе, так как ведет не только к срыву графика производства, но и к прямым экономическим потерям в связи с образованием брака, дополнительным затратам энергии при последующих пусках в работу технологической линии, а также с возможным возникновением аварий, пожаров, взрывов. С учетом такой специфичности непрерывного химического производства изначально такие производства организуются так, чтобы материалы в производственной цепочке перемещались от стадии к стадии точно в срок и в нужном количестве.
Чтобы обеспечить синхронизацию всех операций и избежать лишних запасов материалов или перебоев в работе установки из-за недостатка материалов на отдельных участках производственной цепочки устанавливаются выравнивающие буферы. В этих буферах постоянно находится определенное количество материалов, что позволяет сгладить колебания в доставке материалов и обеспечивает синхронную работу всех звеньев производственной цепочки.
Принципы «точно в срок» и «канбан» в непрерывном химическом производстве.
В качестве примера рассмотрим непрерывное производство материала под названием «этаноламин».
Производственная установка создания ценностей в этом процессе представляет собой цепочку последовательного расположенных аппаратов, соединенных между собой трубопроводами (рис. 1).
Сырьевой материал представляет собой сжиженное газообразное вещество, находящееся под высоким давлением. Такое сжиженное газообразное сырье представляет повышенную опасность: в случае прорыва в производственную зону может возникнуть пожар, взрыв и токсическое воздействие на персонал. Это налагает повышенные требования к герметичности аппаратов и трубопроводов, поэтому вся система аппаратов и трубопроводов является абсолютно герметичной, что не позволяет проводить визуальное наблюдение за состоянием и перемещением материалов по мере их обработки и превращения в готовый продукт. Контроль за перемещением материалов осуществляется с помощью специальных приборов и датчиков.
Исходные компоненты сырья А и Б со склада сырья подаются по трубопроводам в сырьевые буферы 2 А, Б и смеситель 3, откуда поступают в реактор 4.
В реакторе происходит химическая реакция, в результате которой образуется реакционная масса, состоящая из смеси готовых продуктов моноэтаноламина (МЭА) и диэтаноламина (ДЭА), триэтаноламина (ТЭА), непрореагировавшего сырья и небольшого количества воды. МЭА является основным продуктом производственной линии, то есть процент выработки данного продукта выше, чем других, и старт производства осуществляется при получении заказа именно на этот продукт.
Реакционная масса непрерывно поступает в последующие агрегаты, где проводится отделение непрореагировавшего сырья в поз. 5, удаление воды в поз. 7 и разделение готового продукта на три потока МЭА, ДЭА, ТЭА в поз. 9 и поз. 12. Готовые продукты передаются на склад, откуда осуществляется отгрузка готового продукта потребителям.
Установка снабжена приборами и средствами автоматического контроля и управления всеми агрегатами и материальными потоками. На таких высокоавтоматизированных непрерывных производствах отсутствует ручной труд персонала. Поддержание технологического режима в аппаратах и изменение количества подаваемых материалов осуществляется автоматическими средствами управления процессами.
Для выравнивания потока материалов и сглаживания возможных вариаций в количестве подаваемого сырья и промежуточных материалов линия снабжена сырьевыми буферами 2 А, Б и выравнивающими буферами 6, 8.
Так как в химическом производстве трудно, а иногда невозможно выделить единичное изделие, то для вычисления времени цикла вместо времени создания отдельного продукта целесообразно взять скорость технологического процесса.
Рис. 1. Схема движения материальных потоков создания продукта
- Склад сырья.
- А, Б - сырьевые буферы
- Смешение сырья.
- Блок синтеза продукта.
- Колонна отделения непрореагировшего сырья.
- Промежуточные буферы выравнивания производства.
- Колонна осушки продукта.
- Промежуточные буферы выравнивания производства.
- Ректификационная колонна выделения МЭА.
- Товарный буфер МЭА.
- Промежуточная емкость.
- Блок ректификации и выделения товарных ДЭА и ТЭА.
- Склад товарных продуктов.
Скорость создания совокупного продукта (этаноламинов) - 1,9 т в час. Создание продукта в рассматриваемом технологическом процессе начинается через 3 часа после пуска оборудования синтеза, что достаточно быстро по сравнению со временем обработки заказа. Такая скорость достигается посредством содержания большого количества незавершенной продукции в оборудовании (до 39 т), в том числе исходного сырья в блоке синтеза (9 т) и аминов в остальных аппаратах (30 т). Если не иметь незавершенного производства, то время от начала пуска до начала получения готового продукта составит 20 часов (4 часа на заполнение и пуск блока синтеза, 15 часов на наработку незавершенного производства аминов). В целях снижения запасов незавершенного производства было предложено разделить всю незавершенную продукцию на две группы: количество незавершенной продукции, необходимой для протекания процесса синтеза и создания условий непрерывности процесса, и количество незавершенной продукции, необходимой для сглаживания потока. В ходе анализа было выявлено, что запасы, содержащиеся в реакторе, в выравнивающих буферах и колонне товарного МЭА (поз. 9) служат для создания непрерывного процесса и их необходимо оставить в оборудовании. Запасы, содержащиеся в промежуточной емкости (поз. 11) и в колонне выделения товарных ДЭА и ТЭА (поз. 12) составляют 14,71 т, что составляет половину всего незавершенного производства аминов. От этого количества производство при остановке процесса синтеза может спокойно избавиться. Однако возникает проблема задержки выпуска продукции, и при существующей скорости (1,9 т в час) она составляет около 8 часов, и данная задержка становится значимой для потребителя. Но, так как старт производства осуществляется при получении заявки на моноэтаноламин, то можно освободить промежуточную емкость (поз. 11) и колонну (поз. 12) и время получения основной продукции - моноэтаноламина - будет как и раньше равно 3 часам. Таким образом, объем высвобождаемого незавершенного производства составляет 14,7 т, что составляет 50% от незавершенной продукции аминов.
Управление запасами и синхронизация непрерывного химического производства. Непрерывное производство очень чувствительно к колебаниям количества поступающих материалов по отдельным агрегатам. Непостоянство в подаче материалов может привести к перебоям в работе отдельных агрегатов или к остановке агрегатов. Если произойдет остановка одного из агрегатов в производственной цепочке из-за отсутствия необходимых материалов, это вызовет остановку всех звеньев в цепочке, будет нарушена непрерывность работы. После ликвидации причины останова агрегата потребуется повторный пуск агрегатов в работу. Такая неритмичная работа ведет к потере рабочего времени, накоплению незавершенного производства, перерасходу сырья и полуфабрикатов, дополнительным энергетическим затратам, неритмичности работы аппаратов и персонала.
Поэтому при организации непрерывного производства требуется обеспечить высокую синхронизацию и выравнивание всего производства.
Для синхронизации производства применяется метод «точно в срок». Основной принцип этого метода заключается в том, чтобы материалы на последующие этапы производства с предыдущих этапов доставлялись точно в назначенное время, в необходимом количестве и не создавались при этом избыточные запасы материалов и деталей. Информационной системой по отношению к системе «точно в срок» является канбан.
Изначально слово «канбан» означало специальную карточку, которая использовалась для информирования поставщика о необходимости начала производства или поставки деталей заказчику.
По мере внедрения системы «канбан» как средства синхронизации и выравнивания производства она (система), претерпела видоизменения, например, роль канбана стала выполнять тележка [2] для транспортирования деталей между смежными рабочими местами. Пустая тележка сигнализировала, не только об отсутствии деталей, но и о необходимости загрузки и транспортировки деталей на смежный участок. Такая система эффективна в поточных производствах.
Для синхронизации непрерывного производства необходимо наличие буферных запасов сырья, материалов, деталей, готовой продукции.
Такой подход, на первый взгляд, противоречит фундаментальному принципу бережливого производства: не создавать лишних запасов сырья, материалов, деталей на складах и производственных участках. Но бережливое производство это также производство, которое работает ритмично, без сбоев и остановок, которые ведут к потерям рабочего времени, дополнительным затратам энергии, а также к срыву сроков поставок и образованию бракованной продукции.
Обеспечить ритмичность и бесперебойность непрерывного производства можно при наличии определенных буферных запасов сырья и промежуточных материалов или полуфабрикатов, то есть при наличии определенного количества незавершенного производства.
В рассматриваемом нами непрерывном химическом производстве в цепочку производства продукции встроены сырьевые (поз. 2А, 2Б) промежуточные или выравнивающие буферы (поз. 6, 8), снабженные измерительными и информационными системами, которые играют роль канбанов.
Принципы формирования буферных запасов при непрерывном производстве. При определении необходимого количества буферных запасов в бережливом производстве необходимо исходить из следующих постулатов.
1. Запасы должны быть минимальные, чтобы не омертвлять капитал, вложенный в сырье и в затраты на производство полуфабрикатов и готового продукта, законсервированные в буферных запасах.
2. Буферные запасы необходимо иметь в таких количествах, чтобы в течение определенного времени обеспечить бесперебойность работы производственной цепочки при останове какого-либо звена, или перевод ее в режим бережливого останова.
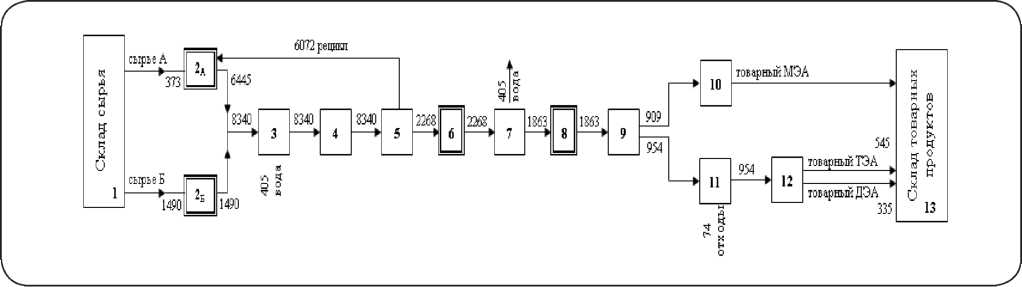
Рис. 2. Схема движения материальных потоков, кг/час
Таким образом, необходимо соблюсти баланс экономической целесообразности при бережливом производстве между потерями из-за замораживания финансовых и материальных ресурсов в буферных запасах и потерями из-за неритмичности и перебоев в работе производственной цепочки в условиях отсутствия буферных запасов.
Исходя из этого, расчет буферных запасов производится по формуле, предложенной авторами Б.Е. Недбайлюком и В.Н. Кудряшовым:
V = V • Т, (1)
з о о’ v '
где V - объем буферного запаса, т; V - скорость материального потока через буфер, т/час; То - минимальное допустимое время безопасной и бережливой работы производственной линии при непредвиденной остановке какого-либо участка, час.
Минимальное допустимое время безопасной и бережливой работы производственной линии при непредвиденной остановке какого-либо участка в каждом конкретном случае обосновывается применительно к рассматриваемой производственной линии, исходя из необходимости обеспечения безопасности работы линии и времени, необходимого для выяснения причины остановки и перехода линии в ожидающий режим работы.
На рис. 2 представлена схема движения материальных потоков по производству этаноламинов (рис. 2) с указанием скорости движения потоков и объемов буферных запасов.
Для рассматриваемой в нашем примере производственной линии (рис. 1): Т = 1,2 часа. В соответствии с формулой (1) для данной установки буферные запасы для сырьевых и промежуточных выравнивающих буферов установлены в следующих размерах:
Буфер 2А V = 9 т Буфер 6 V3 =2,5 т Буфер 8 V = 2,5 т
Для сырьевого буфера запас равен 0 т, так как сырье находится в этом буфере только при нормальной работе установки.
Система «канбан» в непрерывном химическом производстве. Специфика непрерывного производства такова, что все материалы находятся в постоянном движении в направлении от начала производственной цепочки (подача сырья) до конца цепочки (передача готового продукта на склад). Причем скорость движения материала на различных участках производственной цепочки различная, но постоянная для каждого участка (рис. 2).
Такой ритм работы требует наличия непрерывного потока информации о количестве материала, находящегося в обработке в каждом звене цепочки, о количестве материала, находящегося в буферах и о необходимости передачи материала с предыдущего звена цепочки на следующее звено. Поэтому каждое звено производственной цепочки оборудуется системой сбора и передачи информации о запасах материалов.
Система сбора и передачи информации о запасах материалов представлена на рис. 3. Вид А состоит из следующих устройств:
- измерительное устройство (1) для измерения уровня материала в емкости (5);
- каналы передачи информации (2);
- устройство, записывающее информацию на бумажном носителе или показывающее информацию на шкале или дисплее прибора на пульте управления, и передающее команду на изменение количества передаваемого материала (3);
- устройство, управляющее количеством передаваемого материала на следующую стадию процесса (4).
такая система является фактически тем, что в традиционном машиностроении называется «канбан», только это «автоматизированный канбан». Принципиальное отличие от традиционной системы «канбан» заключается в следующем:
- количество материала определяется автоматически;
Рис. 3. Схема автоматизированной системы «канбан»
1. Устройство для измерения уровня материала.
2. Каналы передачи информации.
3А. Устройство, фиксирующее количество материала, передающее команду на изменение количества передаваемого материала.
3Б. Устройство, фиксирующее количество материала.
4. Устройство, управляющее количеством передаваемо го материала.
5. Емкость с материалами.
- роль карточки выполняет диаграмма прибора, на которой фиксируется наличие материала в аппарате и установлено задание для передачи материала на следующую стадию обработки;
- передача материала на следующую стадию обработки осуществляется автоматически.
Возможен вариант (вид Б, рис. 3), когда автоматически осуществляется только замер количества материала и запись на диаграммной ленте, а команды устройству, управляющему количеством передаваемого материала, задаются оператором на пульте управления или устройство приводится в действие вручную.
Схема рассматриваемой нами производственной линии (рис. 1), оснащенной автоматизированной системой «канбан», представлена на рис. 4.
Все стадии производства, включая буферы, снабжены автоматизированными системами «канбан» с передачей и записью информации на пульте управления.
Принцип «вытягивания». Одним из наиболее значимых принципов бережливого производства является принцип «вытягивания». Его реализация на предприятии позволила бы кардинально сократить потери и повысить его конкурентоспособность. На производственной линии этот принцип частично внедрен, так как выработка продукции начинается только при наличии действующего заказа, а иногда и при поступлении предоплаты. Также ежемесячное подтверждение заказа является неким элементом реализации принципа вытягивания и не допускает значительного перепроизводства продукции.
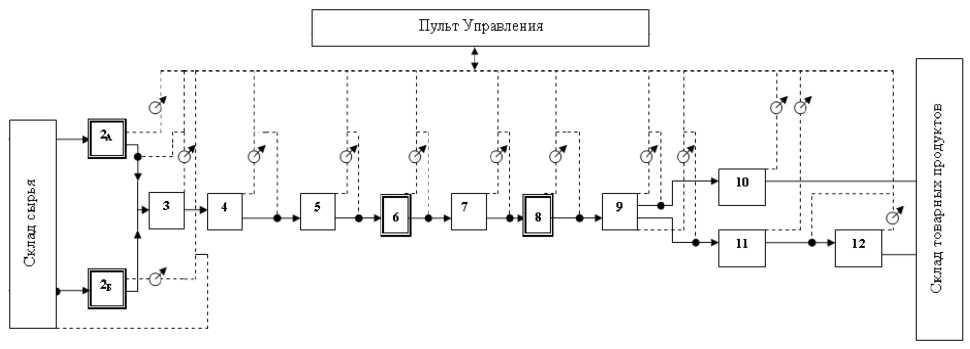
Рис. 4. Схема управления запасами и движением материальных потоков в непрерывном производстве с применением автоматизированных канбанов
Производственная линия работает частично как вытягивающая система, частично как выталкивающая система. Звеном, задающим ритм всей производственной линии, является реактор. Ритм процесса зависит от скорости протекания реакции, поэтому реактор (4) вытягивает необходимое количество материалов из предыдущих стадий 2А, 2Б и 3 для обеспечения необходимой производительности по целевому продукту.
После прохождения компонентов через реактор реакционная масса непрерывно выталкивается на последующие стадии и в дальнейшем продукт выталкивается через все стадии до склада готовой продукции.
Все последующие стадии обязаны принять и переработать поступающие материалы без накопления излишков материалов в буферах выше значений, установленных на основании принципов бережливого производства. такая синхронная работа всех звеньев производственной цепочки обеспечивается путем применения автоматизированной системы канбан в каждом звене для управления материальными потоками.
Управление информацией. Следующим направлением внедрения бережливого производства являются процессы управления информацией. В эти процессы входят процедуры оформления заказов и отгрузка продукции, которые определены специальным регламентом.
Процесс оформления заказов на малотоннажное производство состоит из следующих этапов: регистрация заявки (1-2 дня); виза начальника отдела сбыта (10-30 мин.); подготовка специалистом отдела сбыта служебной записки в производственный отдел и цех исполнитель (30-60 мин.); официальный ответ производственного отдела и цеха (2-3 дня); оформление договора и его визирование всеми заинтересованными службами (7-10 дней); выставление счета на предоплату (5 дней). Максимальный срок подготовки заказа 20 рабочих дней, что является несоразмерным по сравнению со сроком выполнения заказа. Средняя разовая партия продукта - моноэтаноламина - изготавливается в течение 19 часов. С целью сокращения сроков ожидания исполнителя заказа отдел сбыта и производственный отдел вынуждены просить потенциальных клиентов брать на себя дополнительные обязательства - заключать предварительные годовые договоры с указанием приблизительных объемов поставок продукции; ежемесячно подтверждать требуемые объемы поставок за 8-10 дней до конца предыдущего месяца (за это время производственный отдел разрабатывает месячный план и согласовывает график поставки сырья); оплачивать не более чем 5-дневный объем выработки продукции.
Длительный порядок оформления заказов значительно не влияет на эффективность предприятия только в том случае, когда используются 100% производственных мощностей и раскупается 100% вырабатываемой продукции. Однако при спаде производства такие длительные сроки и дополнительные требования к потребителю значительно снижают конкурентоспособность предприятия.
В качестве рекомендации по сокращению сроков оформления заказа мы предлагаем проанализировать необходимость достаточно большого количества согласований при оформлении заказа, а также формирования жесткого месячного плана для малотоннажного производства.
Кроме того, период ожидания исполнения заказа может затянуться и также при поступлении небольшой заявки - меньше минимального объема выработки. Для различных видов продукции этот объем составляет от 2 до 5 т. Это происходит вследствие стремления высшего руководства работать исключительно на отгрузку, т.е. без запасов. Однако, сравнительный анализ затрат на хранение небольшого запаса продукции (немного больше, чем минимальный объем выработки) и потерь от истечения срока годности и возможного ухода клиентов не проводился и, вероятнее всего, будет не в пользу предприятия.
Процесс отгрузки продукции на предприятии состоит из следующих этапов: проверка документов представителя покупателя (5 мин.); согласование отгрузки бухгалтерией (5 мин.); подготовка документов на отгрузку (20 мин.); визирование документов начальником отдела сбыта (10 мин.); подготовка паспорта качества (10 мин.); проезд до места складирования (30 мин.); загрузка продукции (1-2 часа в зависимости от объема); проезд до места взвешивания (20 мин.); взвешивание (2 мин.); коррекция веса (до 1 часа в зависимости от числа коррекций). Максимальный срок отгрузки 4-5 часов. В указанном процессе существует достаточно много потерь, в первую очередь для клиента, что существенно сказывается на его удовлетворенности. Пути сокращения потерь, на наш взгляд, могут быть следующими:
- создание пунктов предварительного взвешивания в местах отгрузки товара - позволит сократить время коррекции веса (до 1 часа);
- сокращение этапов согласования отгрузочных документов, в первую очередь согласование отгрузки бухгалтерией (производство, в основном, начинается после поступления предоплаты).
Принцип организации труда - единая команда операторов. На рассматриваемой производственной установке организовано четыре рабочих мест для ведения производственных операций, которые обслуживают 10 человек в смену. Каждый рабочий знает правила работы не только на своем рабочем месте, но и имеет допуск к работе на других рабочих местах.
Рабочие на данной установке могут обслуживать все агрегаты в производственной цепочке и являются взаимозаменяемыми. Это соответствует духу бережливого производства и позволяет минимизировать трудовые затраты и исключить непроизводительную работу на отдельных участках. Персонал работает как единая команда по принципу «один оператор - несколько функций». Этому способствует также высокая автоматизация производственных операций. Основной функцией персонала является визуальный контроль над ходом процесса по показаниям приборов и ручная корректировка параметров процесса путем задания автоматическим средствам по управлению процессами измененных параметров.
Ручной физический труд применяется только при пусках в работу или при остановах производственной линии и при затаривании готового продукта. Отгрузка готовой продукции осуществляется преимущественно в тару потребителей: металлические бочки, автоцистерны, контейнеры. Возможна отгрузка в железнодорожные цистерны.
Для затаривания продукта не предусматривается специальный персонал, который находился бы в ожидании прибытия транспортного средства потребителя. При необходимости отгрузки продукта эту функцию выполняет один из членов команды операторов, обслуживающих производственную линию. Организация труда персонала по принципу единой команды позволяет снизить затраты труда при производстве продукции.
На предприятии N внедрена интегрированная система менеджмента качества и экологического менеджмента, что позволяет четко выделить основные процессы создания ценности в организации, и может считаться первым этапом внедрения бережливого производства. Принцип СМК - ориентация на потребителя может также считаться прообразом принципа «вытягивания» и при дальнейшем развитии может принести значимые выгоды. Однако необходимо осторожно подходить к полномасштабному внедрению «вытягивания», так как предприятие серьезно ограничено в своих возможностях по изменению месячного объема производства вследствие значительной зависимости от поставщика сырья - монополиста. Кроме того, выявлены значительные временные затраты на оформление заказа и отгрузку продукции, то есть те действия, которые не создают ценность, но необходимы с технологической точки зрения (потери первого рода). Сокращение этих затрат, по нашему мнению, является первоочередной задачей предприятия в рамках системы постоянного улучшения (кстати, предусмотренной СМК). Потери, связанные с наличием незавершенной продукции в переходных емкостях производства, отсутствием весового контроля на отгрузке, а также осуществление контроля качества продукции перед отгрузкой, являются потерями второго рода и подлежат немедленному устранению.
Основными препятствиями на пути внедрения Бережливого производства на химическом предприятии непрерывного цикла могут стать существенная зависимость от поставщика сырья и низкий спрос на побочную продукцию.
Список литературы
- Левинсон У, Рерик Р. Бережливое производство: синергетический подход к сокращению потерь: пер. с англ. А.Л. Раскина; под науч. ред. В.В. Брагина. - М.: РИА «Стандарты и качество», 2007. - 272 с.
- Оно Т. Производственная система «Тойоты». Уходя от массового производства: пер. с англ. - 3-е изд., перераб. и доп. - М.: Институт комплексных стратегических исследований, 2008. - 208 с.