Внедрение пилотного проекта «Бережливое производство» на пищевом предприятии
Системы менеджмента качества (СМК) в соответствии с требованиями стандарта ISO 9001 (который весьма популярен в Казахстане в силу ряда причин, основная из которых — получение доступа к государственным заказам) не дают в большинстве случаев должного эффекта из-за формального подхода к их внедрению. Этому способствует позиция многих органов по сертификации систем, использующих сертификацию для извлечения дохода, что дискриминирует требования стандартов в глазах руководителей, желающих с помощью сертификата получить преференции в борьбе за государственный заказ. Тем не менее получение сертификата не снимает вопроса повышения эффективности управления. Формальное внедрение системы менеджмента не позволяет заглянуть вглубь проблем, сдерживающих повышение конкурентоспособности, так как не концентрирует внимание «на мелочах», в которых, как известно, «прячутся черти».
Сегодня казахстанские предприятия в эффективности деятельности значительно уступают не только компаниям развитых стран, но и компаниям ближайших соседей. Производительность труда от 3 до 5 раз ниже, энергопотребление на единицу продукции в 5—10 раз выше, чем в развитых странах. Не выдерживают многие казахстанские предприятия сравнения с «ближайшими» конкурентами — предприятиями России, Беларуси, Украины.
У многих руководителей отсутствует понимание необходимости изменения мышления и культуры организации деятельности в связи с переходом инициативы от изготовителя к потребителю, а также наблюдается игнорирование факта, что решающая роль в современных концепциях управления перемещается к рядовому исполнителю. Кроме того, не учитывается, что в любом процессе, независимо от отрасли производства, существуют скрытые потери и что определение и устранение этих потерь способно сохранить финансовые средства, сопоставимые с годовым доходом компании.
Анализ деятельности некоторых предприятий показал, что уровень дефектности на отдельных операциях иногда превышает 80%. При этом со стороны высшего руководства не следует никакой реакции, и такое положение считается нормальным. И это при том, что в современном менеджменте борьба с потерями считается основным направлением деятельности менеджеров всех уровней.
В современном менеджменте принято выделять следующие виды потерь, которые увеличивают издержки, не добавляя ценности для потребителя:
- перепроизводство;
- дефекты и переделка;
- нерациональные движения;
- лишняя транспортировка материалов;
- большие запасы;
- излишняя обработка;
- ожидание;
- утеря или отсутствие творческого потенциала.
Эти потери также снижают такой важный для экономики предприятия показатель, как скорость оборачиваемости капитала.
На борьбу с этими потерями нацелен подход, который в русскоязычной литературе получил название «Бережливое производство». Зародившись в середине прошлого века на заводах Toyota, сегодня он проник на предприятия постсоветского пространства, в том числе России, Украины, Беларуси. К сожалению, для подавляющего числа казахстанских предприятий этот подход пока остается неизведанным.
Однако в июле этого года по инициативе Германского общества по техническому сотрудничеству (GTZ) и Программы консультаций для бизнеса (BAS) ЕБРР на базе ТОО ПКФ «Тексти Лайн» был организован семинар-тренинг для казахстанских консультантов, направленный на освоение методов бережливого производства. Семинар был организован с привлечением российской компании «Арсенал Успеха».
На семинаре к участникам пришло понимание того, что бережливое производство — это современный способ организации работы, самый быстрый, гибкий, недорогой и удобный для сотрудников, применяемый многими известными компаниями мирового класса.
Этот подход позволяет (усредненные данные по отраслям промышленности):
- увеличить производительность труда на 35—70%;
- сократить время производственного цикла на 25-90%;
- поднять готовность оборудования до 98%;
- высвободить 25-50% площади;
- уменьшить незавершенное производство на 40-90%;
- сократить складские запасы минимум на 35%;
- снизить потребность в инвестициях на 10-30%;
- сократить сроки реализации инвестиционных проектов на 10-20%.
При этом переход от массового производства к бережливому во многих случаях не требует серьезных вложений. Зачастую отпадает потребность в закупке нового дорогостоящего оборудования, не надо переходить на новые материалы и технологии. Следует «всего лишь» изменить культуру управления предприятием, систему взаимоотношений между различными уровнями и подразделениями предприятия, систему ценностей сотрудников. К сожалению, это сделать иногда труднее, чем найти деньги на закупку новых технологий и оборудования. Здесь важно отметить, что идеология бережливого производства попутно решает многие «неразрешимые» проблемы, свойственные, в частности, казахстанским предприятиям, в том числе вовлечение рабочих в процесс управления.
Бережливое производство направлено против муда.
Муда — японский термин, обозначающий потери, отходы, любую деятельность, которая потребляет ресурсы, но не создает ценности для клиента. Это то, от чего надо избавляться.
Способность видеть муда — это способность видеть потери. Муда присутствует: при производстве изделий, выполнении действий, без которых вполне можно обойтись, перемещении людей и грузов, задержке выполнения операций процесса и т. д. Муда — это те виды потерь, которые были перечислены выше.
Отправная точка бережливого мышления — это ценность. Ценность (товара, услуги) может быть определена только конечным потребителем. Говорить о ней имеет смысл, только имея в виду конкретный продукт (товар или услугу или их совокупность), который за определенную цену и в определенное время способен удовлетворить потребности покупателей. Ценность создается производителем. С точки зрения потребителя, именно ради этого производитель и существует. Внедрение бережливого производства должно начинаться с точного определения ценности в терминах конкретного продукта, имеющего определенные характеристики и цену, чаще всего диктуемую рынком.
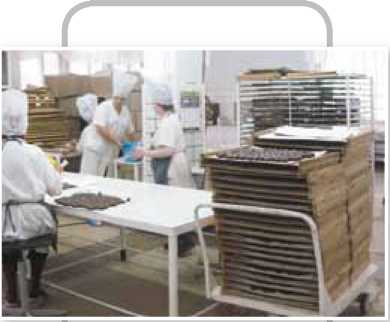
Фото 1. Перепроизводство
Путь к этому — командная работа, переосмысление всей деятельности, связанной с выпускаемыми продуктами, в том числе управленческой. Основная задача — правильно производить нужные продукты. Понятно, что решение этой задачи не под силу одному человеку, какими бы силами и влиянием он не обладал.
Самое сложное — это начать, преодолеть инерцию мышления, по-новому взглянуть на существующую практику, устоявшиеся подходы в управлении.
При этом важно иметь основы знаний о концепции «Бережливое производство», представление о ее инструментах, осознавать наличие кризиса в определенных областях бизнеса, иногда сознательно его обострять, чтобы чувствовать необходимость перемен. Иметь представление о потоках создания ценности и решимость начать немедленную перестройку процессов ее создания.
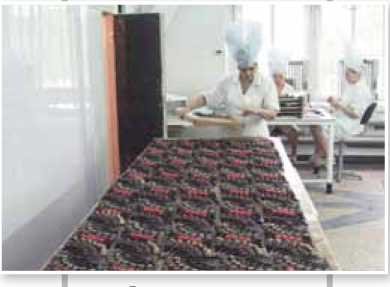
Фото 2. Ожидание
Одно из важных свойств бережливого производства — немедленный результат. Члены команд по улучшениям и все остальные своими глазами должны увидеть, как применение новых методов меняет все вокруг. Важно дать возможность увидеть «поток» и понять, что организация начинает реально меняться.
В соответствии с условиями участия в тренинге каждый участник после завершения обучения должен был реализовать небольшой пилотный проект по применению инструментов бережливого производства на каком-нибудь предприятии.
Для реализации пилотного проекта по согласованию с руководством был выбран участок розничной фасовки АО «Конфеты Караганды». Выбор был обусловлен тем фактом, что на участке — недостаток квалифицированных рабочих, низка производительность труда.
Прежде всего было организовано обучение персонала предприятия, включая менеджеров высшего звена, начальников цехов и мастеров участка. В течение трех дней был проведен семинар, на котором рассматривались философия и инструменты бережливого производства, затем приступили к практической деятельности.
Работа началась с описания потоков создания ценности. После этого занялись поиском и уничтожением муда.
Типичные муда этого участка представлены на фото 1 и 2.
Целью проекта было определено повышение производительности на 20%.
Анализ деятельности участка выявил проблемы, которым следует уделить внимание:
- большое число перемещений работников и значительная доля ручного труда;
- неорганизованность процесса и рабочих мест;
- отсутствие единых стандартов выполнения операций;
- большие запасы продукции, материалов.
Прежде всего было проведено картирование существующего процесса. На этом этапе важно было понять и показать, как протекает процесс (схема 1) и где образуются потери, которые впоследствии были измерены.
С помощью диаграммы «спагетти» были определены перемещение персонала при выполнении операций и сложность этих маршрутов. Выяснилось, что в среднем за один цикл каждый участник проходил расстояние до 100 м, за смену при таком режиме оно составляет от 2,5 до 4 км.
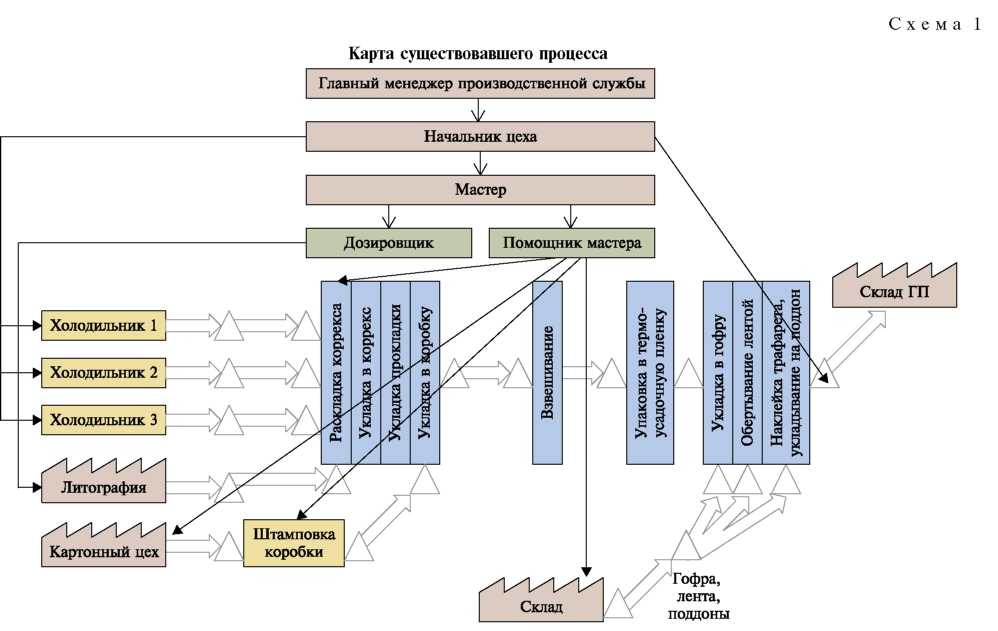
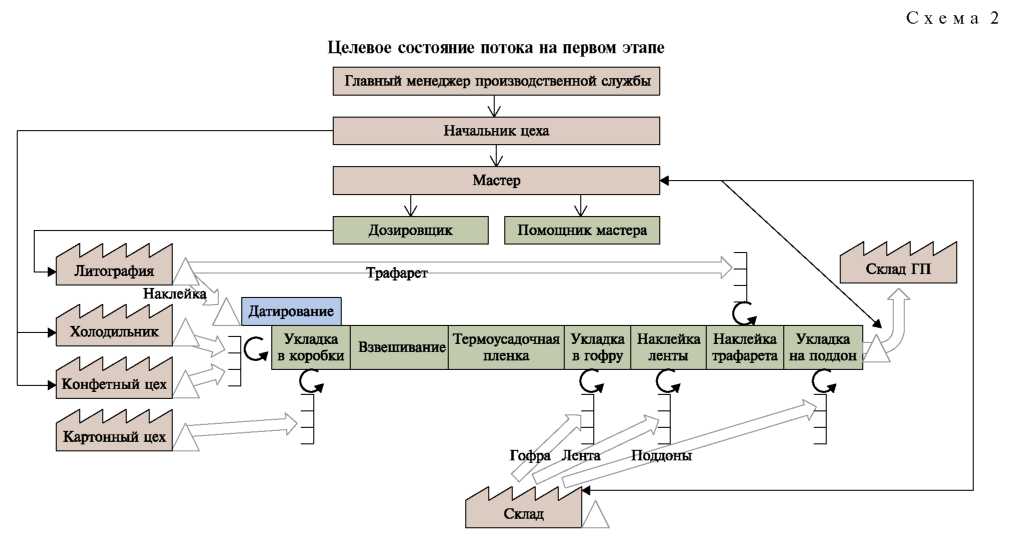
В результате обсуждения было выработано предложение по изменению процесса, составлена карта желательного состояния (схема 2), разработан план его реализации, на основе проведенных измерений определено время такта, выбрана операция, которая представляла наибольшую проблему, и все усилия были сосредоточены на ее улучшении.
Фото 3. Так было: коррексы для укладки конфет разложены на столе и работницы, перемещаясь вокруг стола, заполняют их соответствующими конфетами с подноса, который держат в руке. При этом иногда конфеты падают на пол, что приводит к дополнительным потерям
Фото 4. Так стало: коррексы перемещаются конвейером и работницы заполняют «свои» соответствующие ячейки, не сходя с места
Далее был проведен эксперимент, имитирующий будущее состояние процесса, который подтвердил правильность выбранного решения. В течение последующих двух дней механики цеха изготовили приспособления, наладили конвейер, который позволил избавиться от ненужных перемещений. Были также осуществлены некоторые перестановки оборудования, что дало возможность организовать поток производства единичных изделий.
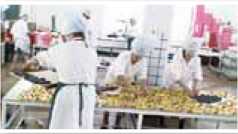
На фото 3 и 4 продемонстрированы ситуации до и после реализации проекта.
В результате проведенных изменений время, затрачиваемое на производство аналогичного числа готовых изделий, сократилось на 22%. Этому способствовало и то, что перемещение продукта сократилось до 36 м. Также снизилось перемещение людей, занятых на укладке. В процессе реализации проекта начаты работы по визуализации процесса, внедрению подхода 5S («Упорядочение»). Кроме того, практически ликвидировались потери от падения конфет, которые составляли около 0,3%.
Если «старым» методом участок мог произвести 1300 готовых изделий в смену, то у «нового» метода потенциал составляет 2300. Чтобы реализовать этот потенциал, необходимо улучшить работу оборудования, внедрив систему ТРМ (всеобщее обслуживание оборудования с участием всего персонала), обучить людей новым стандартам работы, пересмотреть организацию процессов на предыдущих и последующих участках.
Осуществление этого пилотного проекта позволило продемонстрировать его участникам, что методы и инструменты бережливого производства можно применить на данном производстве и что они дают немедленные и вполне ощутимые результаты. Также в процессе работы выяснилось, что люди с удовольствием вовлекаются в этот процесс, дают ценные предложения, с желанием их реализуют. В то же время выяснилось, что они неохотно расстаются с привычными муда, особенно с производственными запасами, полагая, что без этого невозможно гарантировать выполнение плана. Поскольку сразу не получилось выровнять все операции, наблюдалось стремление «забежать» вперед, создавая себе временной запас. Тем не менее общее восприятие было положительным.
Для закрепления полученных результатов в завершение был разработан план мероприятий на ближайшие два месяца. В настоящее время прорабатывается вопрос распространения опыта на другие участки и цеха.